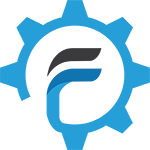
فرمت
محل ارائه خدمت: تهران
شماره تماس: 02191303797
فرمت » ساخت قطعات فلزی » جوشکاری » جوشکاری ذوبی » جوشکاری زیرپودری
تعداد ارائه دهندگان:
محل ارائه خدمت: تهران
شماره تماس:
[UAS_loggedin]
مشاهده
محل ارائه خدمت: مشهد
شماره تماس:
[UAS_loggedin]
مشاهده
محل ارائه خدمت: تهران
شماره تماس:
[UAS_loggedin]
مشاهده
جوشکاری زیرپودری یا جوشکاری قوس مخفی (Submerged arc welding) فرآیند جوشکاری ذوبی است که در آن از کلاف سیم لخت که به موتور متصل است به عنوان الکترود استفاده می شود. سیم جوش از نازل متصل به جریان الکتریسیته عبور می کند، سپس قوس روی نمونه ایجاد شده و عمل محافظت به وسیله پودر جوش انجام می شود. جوشکاری زیر پودری معمولاً در حجم تولید بالا و جوشکاری های ساده استفاده می شود. در مواردی که به جوشکاری های ظریف و پیچیده نیاز باشد از جوشکاری آرگون یا جوشکاری های پرتوی مثل جوشکاری لیزر استفاده می شود.
جوشکاری زیرپودری در صنایع تولید کپسول گاز که تعداد قطعه کار زیاد است، قطعات با ضخامت و طول زیاد مثل صنایع کشتی سازی، ماشین سازی، سازه های فلزی (اسکلت، پل، تیرآهن) و صنایع لوله سازی مورد استفاده قرار می گیرد. به دلیل وجود پودر، جوشکاری قوس مخفی فقط در وضعیت های تخت قابل انجام است. ضمنا به دلیل حرارت ورودی بالا امکان ایجاد اعوجاج در ورق نیز وجود دارد. در فرآیند جوشکاری زیرپودری ایجاد و سوختن قوس زیر لایه ای از پودر جوش انجام می گیرد. پودر جوش در حین پیشرفت جوشکاری به منطقه جوش اضافه می شود. پودر جوشی که نزدیک قوس قرار گرفته ذوب شده و روی سطح جوش ایجاد سرباره می کند. این سرباره از فلز مذاب در برابر اکسیژن و نیتروژن اتمسفر مراقبت می کند. فرآیند جوشکاری زیر پودری قابلیت انجام شدن به وسیله جریان های مستقیم و متناوب را دارد. در صورتی که پارامترهای فرآیند جوشکاری زیر پودری به درستی تنظیم شده باشد، سرباره ایجاد شده به راحتی جدا می شود. بعد از جدا شدن سرباره سطح جوشی که باقی می ماند، عاری از هرگونه پاشش و دود و غیرقابل تمایز با سطح قطعه کار است. تجهیزات فرآیند جوشکاری زیرپودری شامل موارد زیر می باشد. منبع قدرت در فرآیند جوشکاری زیرپودری ترانسفورماتور عادی یا همراه با یکسوکننده است که قابلیت تولید شدت جریان در محدوده 200 تا 2000 آمپر با سیکل تناوب را دارد. مستقیم یا متناوب بودن جریان بستگی به خودکار یا نیمه خودکار بودن فرآیند، جریان و سرعت جوشکاری دارد. همچنین مشخصه ولت آمپر به نحوه کنترل طول قوس بستگی دارد. چنانچه از روش خود تنظیمی استفاده شود ولتاژ ثابت و اگر کنترل به کمک تغییر سرعت راندن سیم جوش انجام شود این مشخصه به صورت آمپر ثابت تنظیم می شود. طیف وسیعی از سیستم های کنترلی در فرآیند جوشکاری زیرپودری وجود دارند. این سیستم های کنترلی شامل سیستم های تنظیم آمپر، ولتاژ، سرعت راندن سیم جوش می شوند. باقی سیستم های کنترلی تنظیم سرعت و جهت حرکت گاری جوشکاری و کمک به شروع قوس و تنظیم نوع و میزان افزایش پودر به جوش زیرپودری را انجام می دهند. حرکت قطعه کار و الکترود نسبت به هم می تواند به چند روش انجام شود. معمول ترین روش در فرآیند جوشکاری زیر پودری سوار کردن الکترود و تجهیزات مربوطه روی گاری و حرکت دادن گاری است. سیستم دیگر شامل نصب الکترود روی یک سری حرکت کننده روی منطقه جوش است. همچنین سیستم هایی وجود دارد که در آن ها الکترود ثابت است و قطعه حرکت می کند. این سیستم ها برای جوشکاری اجزایی مثل سیلندر ها و لوله ها استفاده می شوند. در جوشکاری زیرپودری ترکیب مناسب سیم جوش و پودر جوش روی کیفیت نهایی اتصال تاثیر دارد. هدف نهایی از انتخاب صحیح این مواد ایجاد ترکیب شیمیایی و استحکامی معادل ماده پایه است. سیم جوش در جوشکاری زیرپودری در شکل هایی با مقطع گرد یا تسمه ای یافت می شوند. گرید سیم ها و درصد عناصر آلیاژی آن ها روی خواص مکانیکی و ترکیب شیمیایی جوش تاثیر می گذارد. اغلب سیم جوش های آهنی از فولادهای کم کربن با حداقل گوگرد و فسفر ساخته می شوند. میزان منگنز در این سیم ها متفاوت است و معمولا مقدار آن در کدگذاری الکترودها مشخص می شود. منگنز و سیلیسیم روی استحکام جوش تاثیر می گذارند. همچنین سیم جوش جوشکاری زیر پودری می تواند حاوی درصدی از عناصری مثل نیکل و مولیبدن باشد که روی چقرمگی فلز جوش در دماهای پایین موثر هستند. عناصری که موجب بالا رفتن استحکام و تردی سیم می شوند، از طریق سیم جوش های توپودری به حوضچه مذاب اضافه می شوند. معمولا روی سیم جوش ها یک لایه مس برای افزایش هدایت الکتریکی و جلوگیری از خوردگی افزوده می شود. سیم جوش های تسمه ای برای پوشش دهی فولادهای زنگ نزن استفاده می شوند. به دلیل سطح مقطع عریض این سیم جوش ها، نفوذ آن ها اغلب کم بوده و جوشی صاف و عریض ایجاد می کنند. سیم جوش های تسمه ای برای مصارف تعمیراتی هم استفاده می شوند. پودر جوش در جوشکاری زیرپودری علاوه بر محافظت از حوضچه مذاب و پایداری قوس، قوس را نیز مخفی نگه می دارد. تفاوت آن با جوشکاری الکترود دستی در این است که ترکیبات سلولزی ندارد و طبیعت آن مواد سرباره ساز است. پس محافظت از جوش فقط به وسیله سرباره صورت می گیرد. پودر جوش تأثیر مهمی در کیفیت جوش دارد. پس از تولید پودر جوش باید به اندازه موردنظر دانه بندی شود. اگر پودر خیلی ریز و نرم باشد، گاز نمی تواند از مذاب بیرون رود و تخلخل داخل جوش زیرپودری ایجاد می کند و اگر درشت باشد عمل محافظت به درستی صورت نمی گیرد و جوش زیرپودری با انواع عیوب حاصل می شود. برای تولید پودر جوش از مواد معدنی موردنظر سه روش کلی وجود دارد که در ادامه به آن اشاره می شود. برای تولید پودر جوش در این روش، مواد معدنی، ترکیبات اکسیدی، نمک ها و ترکیبات دیگر به خوبی ریز و آسیاب شده و با نسبت های معین ترکیب می شوند. پس از مخلوط کردن این مواد چسب مناسب اسپری می شود. معمولاً از چسب های سیلیکات سدیم و سیلیکات پتاسیم استفاده می شود. بعد از مخلوط کردن مواد با چسب به مقدار کافی، مخلوط حاصل شده در هوا خشک می شود. این مرحله مواد به صورت کلوخه ای شکل درمی آیند. بعد از خشک شدن، باید عملیات پخت در دمای حدود 350 درجه سانتی گراد روی آن انجام گیرد. در نهایت کلوخه ها خرد شده و با توجه به دانه بندی موردنظر الک می شوند . در این روش می توان عناصر آلیاژی به پودر جوش اضافه کرد اما در روش پودر جوش چسبانده شده در جوشکاری زیرپودری قابلیت بازیافت زیادی ندارد و نسبت به جذب رطوبت بسیار حساس است. در این روش برای تولید پودر جوشکاری زیرپودری ابتدا مواد اولیه آسیاب شده و با نسبت های مختلف ترکیب می شود، سپس مواد چسبنده سرامیکی به آن اضافه می شود. اصلی ترین تفاوت این فرآیند با فرآیند قبلی در دمای انجام عملیات پخت است. دما در این روش حدود 800 تا 900 درجه سانتی گراد است. در ضمن هم زدن حرارت هم به آن داده می شود به حدی که برخی ترکیبات که نقطه ی خمیری شدن پایین تری دارند، در سطح خمیری شده و دانه های دیگر به آن می چسبد. این ترکیب بعد از سرد شدن، در صورت نیاز آسیاب شده و سپس دانه بندی می شود. مواد اولیه جوشکاری زیرپودری با نسبت های مختلف به صورت کلوخه ای داخل کوره قرار می گیرد تا ذوب شود، سپس مذاب داخل آب یا هوا خنک می شود. پس از سرد شدن ترکیب حاصل خرد شدن و دانه بندی انجام می شود. مزیت های این نوع پودر جوش سهولت نگه داری، ترکیب شیمیایی یکنواخت، قابلیت بازیافت و سرعت بالای جوشکاری با آن است. اما این روش قابلیت اضافه کردن عناصر آلیاژی از جمله اکسیژن زداها و فروآلیاژ ها را ندارد. زیرا احتمال بروز جدایش حین فرآیند ذوب کردن پودر وجود دارد. عناصر اصلی ترکیب شیمیایی پودر در جوشکاری زیرپودری شامل ترکیباتی مثل SiO2 ، MnO ، CaO و CaF2 می باشد. پایداری قوس توسط اضافه کردن کمی اکسید پتاسیم بهبود می یابد. می توان برای دستیابی به گرانروی بهتر یا اکسیژن زدایی بیشتر عناصر دیگری نیز به پودر جوش اضافه کرد. پودر جوش استفاده شده در فرآیند جوشکاری زیرپودری می تواند روتیلی، اسیدی یا قلیایی باشد. پودر جوش های روتیلی و اسیدی جوش تمیز تری تولید میکنند اما خواص مکانیکی ضعیف تری نسبت به پودر جوش بازی دارند. همانند سایر روش های جوشکاری، متغیر های فرآیند جوشکاری زیر پودری نیز روی خواص نهایی جوش تاثیر دارند. این متغیرها عبارت از موارد زیر هستند. در جوشکاری زیرپودری سرعت جوشکاری روی نفوذ و پهنای جوش تاثیر دارد. جوشکاری با سرعت بالا جوشی نازک با عمق نفوذ کم ایجاد می کند. سرعت بسیار بالای جوشکاری موجب ایجاد عیوب آندرکات، حفره، عیوب ریشه ای، ذوب ناقص و وزش قوس می شود. سرعت پایین جوشکاری باعث تولید جوشی قارچ شکل می شود. سرعت جوشکاری زیر پودری چنانچه بسیار پایین باشد، جوش حاصل بسیار پهن بوده و ایجاد سطح اتصالی ناصاف و آخال سرباره ای می کند. در جوشکاری زیرپودری قطبیت جوشکاری نیز روی عمق نفود تاثیر می گذارد. اگر سیم تغذیه مثبت باشد، عمق نفوذ بیشتر از هنگامی است که سیم قطب منفی باشد. قطبیت منفی برای زمانی استفاده می شود که هدف پوشش دهی است. ولتاژ قوس نیز چنانچه بالا باشد جوشی پهن با نفوذ کم تولید می کند. ولتاژ بالا برای جوشکاری زیرپودری پخ های پهن و افزایش ورود عناصر آلیاژی از پودر جوش مناسب است. ولتاژ بالا موجب افزایش مصرف پودر جوش و دشوار شدن جدا کردن سرباره نیز می شود. جریان جوشکاری زیرپودری رابطه مستقیم با نرخ رسوب دهی و عمق نفوذ جوشکاری دارد. اما جریان های خیلی بالا موجب ایجاد آندرکات، تحدب زیاد جوش، سوختگی و ترک حرارتی می شود. در جوشکاری زیرپودری ، سیم جوش های نازک عمق نفوذ بیشتر و پایداری قوس بهتری در مقایسه با سیم جوش های ضخیم تر دارند. با این وجود چنانچه جوش پهن مد نظر باشد از سیم جوش های ضخیم استفاده می شود. طراحی پشت بند جوشکاری زیرپودری نیز برای مواردی که عمق نفوذ کامل نیاز است، از اهمیت بالایی برخوردار است. این پشت بند ها مانع جریان یافتن مذاب به پشت درز جوش می شود. پشت بند ها انواع مختلفی دارند که شامل پشت بند های تسمه ای، مسی، پودری و سرامیکی می شوند. همچنین می توان از یک پاس جوش با الکترود دستی به عنوان پشت بند استفاده کرد. با توجه به قدرت نفود خوب جوش زیرپودری می توان ورق هایی با ضخامت کمتر از 32 میلیمتر را بدون پخ سازی لبه ها جوش داد. به علت مخفی بودن قوس به عینک ها و وسایل افزایش ایمنی خاصی نیاز نیست. به علت زیاد بودن نرخ رسوب فرآیند جوشکاری زیرپودری سرعت جوشکاری بالا است. سطح جوش حاصل از جوش زیرپودری به دلیل نبودن پاشش و خواص اکسیژن زدایی و تمیز کاری پودر تمیز است. به دلیل عدم تعویض الکترود ظاهر جوش یکنواخت است و کیفیت خوبی دارد. از معایب جوشکاری زیرپودری می توان به محدودیت وضعیت جوشکاری و احتمال اعوجاج قطعات اشاره کرد. تمیز کردن سرباره نیز زمان بر بوده و احتمال محبوس شدن سرباره در حوضچه مذاب وجود دارد. هزینه جوشکاری زیرپودری وابسته به هزینه الکترود و پودر جوش مورد استفاده است. به طور کلی جوشکاری زیرپودری فرآیندی مقرون به صرفه و پر استفاده است. چنانچه اضافه کردن عناصر آلیاژی خاصی به حوضچه مذاب مد نظر باشد، استفاده از پودر جوش های خاص و الکترودهای توپودری لازم می شود که هزینه جوشکاری زیرپودری را افزایش می دهد. در مقایسه با سایر فرآیند های جوشکاری، هزینه جوشکاری زیرپودری تنها از جوشکاری الکترود دستی بیشتر است.تجهیزات فرآیند جوشکاری زیرپودری
منبع قدرت جوشکاری زیر پودری
سیستم های کنترلی و تنظیم حرکت
مواد مصرفی جوشکاری زیرپودری
سیم جوش زیرپودری
پودر جوش زیرپودری
پودر جوش چسبانده شده
پودر جوش آگلومره شده
پودر جوش پیش ذوب شده
ترکیب شیمیایی پودر جوش
متغیر های فرآیند جوشکاری زیرپودری
سرعت جوشکاری زیرپودری
قطبیت جوشکاری زیرپودری
ولتاژ قوس ریزپودری
جریان جوشکاری زیرپودری
ضخامت سیم جوش زیرپودری
طراحی پشت بند برای جوشکاری زیرپودری
مزایا و معایب جوشکاری زیرپودری
هزینه جوشکاری زیرپودری
فرمت یک راه حل نوین جهت رفع نیازهای صنعتی است. هدف فرمت ایجاد بستری برای معرفی، بررسی و مقایسه ی خدمات صنعتی ارائه شده توسط ارائه دهندگان مختلف و انتخاب بهترین راه حل جهت رفع مشکلات و پاسخگویی به نیازهای صنایع مختلف است.
آدرس: تهران، خیابان آزادی، دانشگاه صنعتی شریف
ایمیل: info@formmat.ir