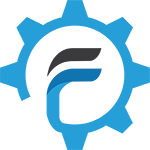
فرمت
محل ارائه خدمت: تهران
شماره تماس: 02191303797
فرمت » ساخت قطعات فلزی » ماشینکاری » تراشکاری » دنده زنی
تعداد ارائه دهندگان:
محل ارائه خدمت: تهران
شماره تماس:
[UAS_loggedin]
مشاهده
محل ارائه خدمت: تهران
شماره تماس:
[UAS_loggedin]
مشاهده
محل ارائه خدمت: اصفهان
شماره تماس:
[UAS_loggedin]
مشاهده
دنده زنی یا دنده تراشی به مجموعه ای از فرایندها گفته می شود که عمل ساخت دنده روی قطعه استوانه ای را به وسیله فرایندهای ماشین کاری، شکل دهی یا برشکاری انجام می دهند. به طور کلی، ساخت دنده در صنعت به وسیله طیف گسترده ای فرایندها از قبیل ریخته گری ، مهرزنی و متالورژی پودر انجام می شود. اما ساخت دنده به این شکل، بیشتر برای کاربردهای سبک با مقاومت به سایش پایین و دقت ابعادی پایین انجام می شود. هر وقت که کاربرد مد نظر نیاز به تقویت کاربرد چرخ دنده داشته باشد، از فرایندهای دنده زنی استفاده می شود.
در تمامی فرایندهای تولید چرخ دنده ، شامل تولیدات ظریف و با تناژ پایین و تولیدات حجیم، مراحل دنده زنی شامل چهار فرایند اصلی بلنک زنی، ماشین کاری یا برش دنده، عملیات حرارتی و سپس پرداخت دنده می شود.
بلنک زنی یا ساخت بلنک به فرایندهای اولیه فرم دهی یا ماشین کاری گفته می شود که قطعه ای نیمه آماده را برای فرایند تولید چرخ دنده فراهم می کنند. تراشکاری با ماشین تراش یا دستگاه های فرز CNC به همراه رو تراشی ، تنظیم دقیق شفت ها و گاهی اوقات نیز سنگ زنی در این فرایند جا میگیرند. بلنک های با کیفیت، تاثیر مهمی روی کیفیت نهایی دنده ها دارند.
ماشین کاری، هابینگ، شیپینگ، خان کشی و شیوینگ جزو پرکاربرد ترین فرایندهای برش یا ساخت دنده در بلنک های از پیش آماده هستند. انتخاب بین این فرایندها به متغیرهای فرایند تولید از قبیل استاندارد های کیفی، حجم تولید و شرایط اقتصادی بستگی دارد.
تولید چرخ دنده
فرایندهای دنده زنی ، وابسته به نوع فرایند، قبل یا بعد از اعمال عملیات حرارتی روی قطعه انجام می شوند. لازم به ذکر است که پیش از عملیات حرارتی، قطعه هنوز نرم و آماده ماشین کاری است و بعد از عملیات حرارتی، قطعه به استحکام و سختی بالا میرسد. طی عملیات حرارتی، استحکام و دوام چرخ دنده برای تحمل بارگذاری و سایش شدید بیشتر می شود، اما دقت ابعادی و هندسی خود را از دست می دهد. تحولات متالورژیکی انجام شده روی چرخ دنده موجب اعوجاج ساختار آن و کاهش کیفیت چرخ دنده می شود. در این مرحله، انجام سنگ زنی های بسیار دقیق روی سطح داخلی و خارجی چرخ دنده برای به دست آوردن دوباره دقت ابعادی و پرداخت سطح مد نظر لازم میشود.
دنده تراشی
دنده زنی با ابزار فرزکاری یا form milling، خانکشی یا broaching، شیپینگ و هابینگ از فرایند های برش و ماشین کاری در تولید چرخ دنده هستند. شیوینگ، لپینگ و هونینگ از فرایندهای پرداخت در تولید چرخ دنده به شمار می روند.
در دنده زنی به روش فرزکاری از ابزاری دایره ای با چندین دنده استفاده می شود که شکلی مشابه فضای بین دنده ها دارد. این ابزار به شکل شعاعی روی بلنک دنده تغذیه می شود و به سمت مرکز بلنک حرکت می کند تا دنده مدنظر ایجاد شود. میزان فرو روی ابزار روی بلنک، به عمق و شعاع دنده نهایی بستگی دارد.
شماتیکی از دنده زنی به روش فرزکاری
دنده زنی با این ابزار روش ساده و انعطاف پذیری برای دنده تراشی و ماشین کاری چرخ دنده ها است. در این روش ، تجهیزات و ابزار مورد نیاز نسبتا ساده هستند و از ابزار ماشین کاری استاندارد استفاده می شود. با این وجود، در این روش، سرعت بسیار کم است و حفظ دقت ابعادی مد نظر به مهارت بالایی نیاز دارد. بنابراین این روش دنده زنی فقط در تولیدات با تناژ بسیار پایین استفاده می شود. به خصوص هنگامی که نیاز به تولید دنده های با ساختار مخروطی وجود دارد پیچیدگی فرایند بسیار بالا می رود. فرایندهای تولید چرخ دنده با فرزکاری نیمه اتوماتیک نیز وجود دارند، که هزینه های اپراتور و در نتیجه هزینه فرایند و دقت ابعادی تولید را بالا می برند.
دنده زنی به روش خان کشی روشی با دقت ابعادی بالا برای ایجاد دنده های داخلی در قطعه است. در این روش، همه دنده ها به صورت همزمان بریده شده و به صورت مداوم ایجاد می شوند. در این روش، ایجاد دندانه ها دقت ابعادی بالایی دارد، هر چند به منظور ایجاد هر مجموعه دندانه با ابعاد معین باید ابزار مجزایی تهیه شود. ابزار خان کشی معمولا پرهزینه است و هزینه دنده زنی را بالا میبرد، بنابرین این روش برای تولیدات با تناژ بالا به صرفه است. گاهی ابزار خانکشی بخشی نیز در انتهای خود به منظور پرداخت نهایی دارد که پرداخت بسیار صافی تولید می کند. در این فرایند، ابزار معمولا به صورت خطی نسبت به قطعه کار حرکت می کند و قطعه کار معمولا ثابت است.
خان کشی
فرایند دنده تراشی خان کشی برای دنده های خارجی نیز انجام می شود که به فرایند خان کشی پات مشهور است. در این فرایند، چندین ابزار خان کشی دارای شیارهای داخلی به صورت پشت سر هم توسط نگه دارنده نگه داشته می شود. قطعه از درون این شیار ها رد شده و فرایند انجام می شود. فرایندهای خانکشی قابلیت ایجاد 250 چرخ دنده را در ساعت دارند.
به منظور دنده زنی با فرایند شیپینگ ، کاتر شکلدهی دنده و بلنک، روی شفت های خود به صورت مناسب تعبیه می شوند. در این فرایند ، چیدمان فرایند باید به شکلی باشد که کاتر و بلنک با سرعت همسان نسبت به یکدیگر بچرخند. در شروع فرایند، کاتر با حرکت عمودی با بلنک هم ارتفاع شده و با حرکت شعاعی به سمت مرکز بلنک حرکت می کند. هنگامی که عمق دندانه مد نظر ایجاد شد، کاتر و چرخ دنده ساخته شده به آرامی از یکدیگر دور می شوند.
شیپینگ
در این فرایند دنده زنی ، کاتر از فولاد HSS ساخته شده که اغلب با لایه ای از نیترید تیتانیوم لایه نشانی شده با فرایند PVD پوشانده شده است. این فرایند قابلیت تولید چرخ دنده هایی با شکل های مستقیم و مارپیچ را دارد. در حالت مارپیچ، حرکت کاتر و بلنک نسبت به هم، کمی پیچیده تر می شود. در ضمن در برخی از سیستم های شیپینگ قابلیت دنده تراشی تعداد بالایی چرخ دنده به صورت همزمان وجود دارد. این سیستم را می توان روی دستگاه های CNC نیز سوار کرد.
در فرایند شیپینگ ، ایجاد دنده های با ساختار پیچیده نیاز به حرکت های پیچیده کاتر و بلنک نسبت به هم دارد که مشکلات متعددی ایجاد می کند. در فرایند دنده زنی با هابینگ ، ساختار دنده های پیچیده به وسیله ابزاری استوانه ای انجام می شود که روی آن دنده های مد نظر تعبیه شده اند. روی این استوانه، دنده ها به صورت مارپیچ ایجاد شده اند و بین آن ها شیارهایی تعبیه شده است. هابینگ ، فرایندی اقتصادی و بسیار سریع است که بیشترین کاربرد را بین فرایندهای مختلف دنده تراشی دارد. به وسیله دنده تراشی با هابینگ میتوان اسپلاین یا هزار خار و چرخ زنجیر را نیز تراشکاری کرد. با افزایش ردیف های دندانه های هاب سرعت تولید فرایند هابینگ بالاتر می رود، اما دقت ابعادی پایین تر می آید.
هابینگ
شیوینگ پرکاربرد ترین فرایند برای انجام پرداخت نهایی در مراحل دنده زنی است. شیوینگ به وسیله ابزاری به شکل چرخ دنده انجام می شود که دقت ابعادی بالایی دارد. سر هر دنده ابزار شیوینگ ، لبه های نوک تیز تعبیه شده است که فرایند پرداخت را با دقت زیادی انجام دهد.
شیوینگ
در پرداخت دنده تراشی به روش شیوینگ ابزار و چرخ دنده نسبت به همدیگر حرکت می کنند تا براده برداری بسیار ظریفی از روی دنده های چرخ دنده انجام شود. این فرایند کم تر از یک دقیقه طول می کشد و سطح بسیار صافی روی دندانه ها به جا میگذارد. ابزار های شیوینگ هر چند قیمت بالایی دارند، اما به دلیل بار کمی که حین فرایند تحمل می کنند، عمر نسبتا بالایی نیز دارند. چنانچه امکانات موجود شرایطی را فراهم کند که عملیات حرارتی بدون ایجاد اعوجاج در قطعه انجام شود، شیوینگ را می توان پیش از سختکاری انجام داد.
لپینگ به وسیله چرخ دنده های چدنی انجام می شود که روی آن جریانی از ذرات بسیار ریز خراشان سیال در روغن جاری شده است. میزان ماده ای طی فرایند لپینگ حذف می شود، بسیار کم است. بنابراین از این فرایند معمولا در آخرین مرحله دنده زنی پس از پرداخت اولیه و سخت کاری استفاده میشود.
لپینگ
هونینگ فرایند پرداخت نهایی دیگری است که به وسیله چرخ دنده های مارپیچ یا کرمی شکل انجام میشود. چرخ دنده های هونینگ گاهی اوقات از فولادی ساخته میشوند که روی دندان های آن ذرات ریز کاربید سمانته یا الماس تعبیه شده است. در بسیاری موارد نیز از چرخ دنده های پلاستیکی استفاده می شود که این ذرات روی آن قرار گرفته است. پلاستیک نسبت به فولاد ارزان تر است و انعطاف پذیری بالایی دارد. ابزار هونینگ در دنده زنی به چرخ دنده فشار وارد می کند و عمل پرداخت نهایی را به این شکل انجام می دهد. هونیگ نسبت به لپینگ گران تر بوده اما فرایند بسیار سریعتری می باشد.
هونینگ
هزینه دنده زنی در مرحله اول بستگی به نوع فرایند دارد. برخی از فرایندهای یاد شده ماننده شیپینگ زمان بیشتری برای چیدمان ابزار و شروع فرایند نیاز دارند که موجب افزایش هزینه دنده زنی می شود.. برخی از فرایندها ابزار بسیار کم هزینه ای دارند مانند فرزکاری که موجب کاهش قابل توجهی در هزینه دنده زنی می شوند. برخی از فرایندها نیز به صورت کاملا اتوماتیک و تحت سیستم های CNC انجام می شوند که هزینه دنده زنی را پایینتر میاورند. همه این پارامترها در انتخاب فرایند نقش موثری دارند. در مرحله بعد، ماده سازنده قطعه کار هزینه دنده زنی را تعیین می کند. هر چه ماده سازنده سخت تر باشد، نیاز به ابزار مستحکم تری وجود دارد که در نتیجه هزینه دنده زنی بیشتر میشود.
فرمت یک راه حل نوین جهت رفع نیازهای صنعتی است. هدف فرمت ایجاد بستری برای معرفی، بررسی و مقایسه ی خدمات صنعتی ارائه شده توسط ارائه دهندگان مختلف و انتخاب بهترین راه حل جهت رفع مشکلات و پاسخگویی به نیازهای صنایع مختلف است.
آدرس: تهران، خیابان آزادی، دانشگاه صنعتی شریف
ایمیل: info@formmat.ir