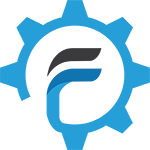
فرمت
محل ارائه خدمت: تهران
شماره تماس: 02191303797
فرمت » عملیات قبل/بعد از ساخت » عملیات حرارتی » سخت کاری » سخت کاری پلاسما
تعداد ارائه دهندگان:
محل ارائه خدمت: تهران
شماره تماس:
[UAS_loggedin]
مشاهده
محل ارائه خدمت: تهران
شماره تماس:
[UAS_loggedin]
مشاهده
محل ارائه خدمت: کرج
شماره تماس:
[UAS_loggedin]
مشاهده
سخت کاری پلاسما از روش های مهم بهبود خواص سطح فلزات می باشد و جزو روشهای نیتروژن دهی است، به همین دلیل به سخت کاری پلاسما ، نیتروژن دهی پلاسما هم گفته می شود. در فرآیند سختکاری پلاسما ، نیتروژن به اجزای سطح نفوذ میکند. محدوده دمایی این فرآیند 400-570 درجه سانتی گراد می باشد و طی آن، مقاومت سایشی ، مقاومت خوردگی و عمر خستگی قطعات فلزی افزایش می یابد. این فرآیند اغلب در پلاسمای گازهای نیتروژن و هیدروژن انجام میپذیرد.
الکترون های آزاد کاتد (قطعه کار) با اعمال ولتاژ، از سطح کاتد به طرف آند (دیواره محفظه) شتاب میگیرند و با مولکولهای گاز نزدیک کاتد برخورد می کنند. این مولکول ها در اثر این برخورد میشکنند. در فرایند سختکاری پلاسما ، اتم های گاز، الکترون های لایه ظرفیت خود را آزاد می کنند و پدیده یونیزاسیون اتفاق می افتد. در اثر این پدیده، یون های مثبت نیتروژن به طرف کاتد و الکترون های اتم نیتروژن ، با بار منفی به طرف آند حرکت می کنند. به این ترتیب با برقراری جریان، پلاسما تشکیل میشود و عملیات سختکاری به روش نیتروژن دهی پلاسمایی انجام می شود.
طی عملیات سخت کاری پلاسما ، یون های مثبت نیتروژن با اتم های آهن واکنش داده و به طرف کاتد شتاب می گیرند. یک لایه نیتریدی ، متشکل از لایه سفید و لایه نفوذی، روی سطح قطعه تشکیل می دهند. این روش در مقایسه با دیگر روش های سختکاری سطحی، حداقل تغییر شکل برشی را ایجاد می کند و با کنترل ابعادی مناسبی به انجام میرسد. همچنین سطوح سخت کاری شده می توانند سخت تر از سطوح کربن دهی شده باشند و تا دمای نیتروژن دهی کاملاً پایدار هستند. عملیات سخت کاری توسط فرایند نیتروژن دهی ، در سال 1923 توسط دکتر آدولف فری ابداع شد. پس از جنگ جهانی دوم، این روش به صورت صنعتی در ژاپن بکار گرفته شد. روش سختکاری پلاسما به ویژه برای قطعات خودرو یا هواپیما نظیر سیلندر یا شیرآلات خروج دود که در دمای بالا، فشار بالا و سرعت بالا کار می کنند، مناسب است. در این روش به عملیات سخت گردانی بعدی نیاز نیست و سختی قطعه تا دمای 650-600 درجه سانتی گراد نیز حفظ میشود. قبل از انجام نیتروژن دهی باید تمامی عملیات از جمله عملیات حرارتی ، ماشینکاری و سنگ زنی انجام شود. از روش سختکاری پلاسما، معمولاً برای نیتراته کردن سطح فولادهای متوسط کربن و آلیاژی استفاده می شود که دارای عناصری باشند که قابلیت تشکیل نیترور را داشته باشند مانند Al، Cr، Mo، V. ضخامت لایه سخت شده در روش سخت کاری پلاسما، معمولاً 0.2 تا 0.4 میلی متر است و مدت زمان رسیدن به این عمق، با توجه به پایین بودن دما در مقایسه با روش های دیگر سختکاری ، بیشتر است. اساس دستگاه سخت کاری پلاسمایی شامل محفظه خلاء، منبع تغذیه، سیستم گاز شامل صفحه ترکیب گاز و تجهیزات کنترل جریان گاز است. برای اطمینان از عایق بودن قطعه کار از محفظه خلاء فیکسچرهای خاصی به کار برده می شود. برای کاهش زمان این فرایند، تجهیزات گرم کننده و خنک کننده اضافی هم به سیستم اضافه می شود. طبق شکل بالا که نمایی از دستگاه نیتروژن دهی پلاسما است، محفظه برای تأمین خلاء وجود دارد و در اکثر موارد دارای دیواره دوجداره ای است که توسط آب خنک می شود. محفظه افزایش دمای قطعات درون کوره پلاسما ، به سه روش جریان های همرفتی ، تابش و حرارت مستقیم با کمک پلاسما انجام می شود. این عملیات با تولید گونه های فعال خاص باعث می شود تا واکنش های شیمیایی و تغییرات فیزیکی درسطح رخ دهد که با روش های دیگر غیرممکن است. از جمله عواملی که بر فرآیند سخت کاری پلاسما تاثیر می گذارند می توان به دمای قطعه، زمان عملیات، ترکیب گاز درون محفظه، دبی گاز ورودی به محفظه، فشار موجود در محفظه، ولتاژ، فرکانس، چرخه کاری و چگالی جریان پلاسما اشاره کرد. بطور کلی، فولادهای زیر را می توان برای کاربردهای خاص تحت عملیات حرارتی نیتروژندهی قرار داد : 1. فولادهای کم آلیاژ آلومینیوم دار 2. فولادهای کم آلیاژ کروم دار با کربن متوسط ( بیش از 25/0 درصد کربن ) 3. فولادهای قالب گرم کار حاوی 5 درصد کروم 4. فولادهای ضدزنگ فریتی و مارتنزیتی 5.فولادهای ضدزنگ آستنیتی 6. فولادهای ضدزنگ سخت شونده رسوبی فولادهای ساده کربنی برای نیتروژن دهی مناسب نیستند. سخت کاری پلاسما فولاد ساده کربنی به معنی تشکیل یک لایه سطحی بسیار ترد است که به سادگی از سطح جدا می شود. به علاوه، افزایش سختی در ناحیه نفوذ نیتروژن در این نوع فولادها کم است. سخت کاری پلاسما از لحاظ جنبه های اقتصادی و فنی، در صنعت مورد توجه قرار گرفته است. محصولات سخت شده تحت این فرآیند کمترین آلودگی و ضایعات را دارند. دستگاه های سخت کاری پلاسما شامل نمونه های ساده آزمایشگاهی تا صنعتی هستند. یکی از علل گسترش سریع این روش، طیف وسیع انواع مواردی است که می توانند با این روش سخت کاری شوند. کیفیت قطعات پس از سخت کاری پلاسمایی با روش های نوینی مانند لایه نشانی به روش CVD و کاشت یونی قابل رقابت است. 1. با کنترل پارامترهای فرایند سختکاری پلاسما ، امکان کنترل فازهای تشکیل شده در سطح وجود دارد. 2. استفاده از این روش در دماهای پایین، امکان پذیر است. این امر به میزان بسیار زیادی از اعوجاج قطعات می کاهد. 3. لایه تشکیل شده طی سختکاری پلاسما منعطف تر است. بنابراین، چقرمگی شکست قطعه کار افزایش می یابد. 4. این روش هیچ ضرری برای محیط زیست ندارد. 5. سطوح سختکاری شده به روش نیتروژن دهی پلاسما ، سختی بالایی دارند. 6. قطعات سختکاری شده به روش نیتروژن دهی پلاسما ، مقاومت خوبی در برابر سایش دارند. 7. قطعات سخت شده به روش سختکاری پلاسما، در برابر خوردگی، به ویژه در آب و بخار آب مقاومت دارند. 8. فلزات قرار گرفته تحت این عملیات مقاومت خوبی در برابر خستگی دارند. 1. فولادهای سخت شده با این روش، فولادهایی مخصوص بوده و گران هستند. 2. قبل از فرآیند، عموماً باید عملیات حرارتی مخصوصی برای ریز کردن دانه های فولاد، انجام گیرد. 3. ضخامت قشر سخت کاری شده بسیار نازک است و از حدود 0.3 میلی متر تجاوز نمی کند. 4. عدم قابلیت تکرارپذیری این فرایند برای قطعات بزرگ 5. مشکل ایجاد دمای یکنواخت در تمامی نواحی قطعه 6. آسیب دیدن سطح به علت بروز قوس 7. مشکل بودن نیتروژن دهی قطعاتی با شکل و اندازه های متفاوت 8. هزینه نسبتاً بالای سرمایه گذاری برای فرایند سختکاری پلاسما موارد مرسوم استفاده از این روش در صنعت عبارتند از: 1. سخت کاری پلاسما ابزارها مانند قالب فورج ، اکستروژن ، قالب های ریخته گری تحت فشار آلومینیم و ریل و بازوهای هیدرولیک 2. استفاده از فرایند سختکاری پلاسما در ساخت ماشین های صنعتی، میله ها، پیستون، شفت، قلاویز و… 3. کاربرد این روش در صنایع خودروسازی، میل لنگ، سوپاپ، دنده های گیربکس، شفت، دنده های پمپ روغن، میل بادامک، سرسیلندر و… فرآیند سختکاری پلاسما در خلاء های نسبتا بالا با استفاده از انرژی و ولتاژ بالا انجام می شود. این فرآیند، یکی از فرآیند های مدرن مهندسی می باشد که از تکنولوژی تخلیه نورانی برای تولید نیتروژن اتمی و نفوذ نیتروژن به سطح قطعه بهره می گیرد. در سخت کاری پلاسما اتمهای نیتروژن به صورت رادیکال و یون در آمده و سپس با شتاب بسیار زیادی به سطح نمونه برخورد میکنند. با بمباران سطح نمونه توسط یونهای نیتروژن و آرگون، سطح قطعه تمیز شده و ترکیبات نیتریدی بر روی سطح ایجاد میشود. در این روش، ترکیب شیمیایی سطح نمونه را میتوان کنترل کرد و تغییرات ناشی از فرآیند سخت کاری پلاسما مانند اعوجاج و تغییر شکل ناگهانی در قطعه را میتوان کاهش داد. این فرآیند در مقایسه با روش های گذشته، فوق العاده از کنترل خوبی برروی اجرای فرآیند برخوردار است. در خدمات نیتروژن دهی پلاسما ، زمان عملیات بعلت وجود پتانسیل اعمالی بر روی نمونه، کم می باشد. سخت کاری قطعه با استفاده از پلاسما یک فرآیند مدرن می باشد در نتیجه هزینه های مربوط به این فرآیند، به صرفه می باشد. هزینه سختکاری پلاسما هم مربوط به دستگاه نیتروژن دهی پلاسما و هم مربوط به هزینه های عملیاتی می باشد. در حال حاضر هزینه دستگاه نیتروژن دهی پلاسمایی در سال 1400، حدود 400 میلیون تومان می باشد و نمونه های ساخت داخل، از لحاظ کیفیت با دستگاه های نیتروژن دهی پلاسما ساخت خارج از کشور تطابق دارد ولی از لحاظ هزینه، قیمت دستگاه سخت کاری پلاسما در داخل نسبت به خارج از کشور بسیار متفاوت تر می باشد. هزینه های عملیاتی فرایند سختکاری پلاسما به چندین دلیل صرفه اقتصادی دارد:ویژگی های سخت کاری پلاسما
دستگاه سخت کاری پلاسمایی
می تواند عمودی و یا افقی قرار بگیرد. بر روی جداره، منافذی برای مشاهده فرایند سخت کاری پلاسما در نظر گرفته می شود. گازهایی که برای سخت کاری پلاسمایی مورد استفاده قرار می گیرند، عبارتند از: نیتروژن ، هیدروژن و گاهی متان. این فرایند در فشار بین (تور) 10-1 انجام می شود.فولادهای مناسب برای فرایند سخت کاری پلاسما
سخت کاری پلاسما در صنعت
مزایای روش سخت کاری پلاسما
معایب سخت کاری پلاسما
کاربرد روش سخت کاری پلاسما
خدمات سخت کاری پلاسما
هزینه سخت کاری پلاسما
فرمت یک راه حل نوین جهت رفع نیازهای صنعتی است. هدف فرمت ایجاد بستری برای معرفی، بررسی و مقایسه ی خدمات صنعتی ارائه شده توسط ارائه دهندگان مختلف و انتخاب بهترین راه حل جهت رفع مشکلات و پاسخگویی به نیازهای صنایع مختلف است.
آدرس: تهران، خیابان آزادی، دانشگاه صنعتی شریف
ایمیل: info@formmat.ir