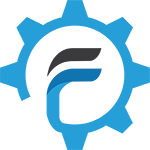
فرمت
محل ارائه خدمت: تهران
شماره تماس: 02191303797
فرمت » ساخت قطعات فلزی » قالب سازی » ساخت قالب فورج
تعداد ارائه دهندگان:
محل ارائه خدمت: اراک
شماره تماس:
[UAS_loggedin]
مشاهده
محل ارائه خدمت: تبریز
شماره تماس:
[UAS_loggedin]
مشاهده
محل ارائه خدمت: تهران
شماره تماس:
[UAS_loggedin]
مشاهده
محل ارائه خدمت: تهران
شماره تماس:
[UAS_loggedin]
مشاهده
محل ارائه خدمت: مشهد
شماره تماس:
[UAS_loggedin]
مشاهده
محل ارائه خدمت: تهران
شماره تماس:
[UAS_loggedin]
مشاهده
ساخت قالب فورج برای آهنگری یا فورجینگ به گونه ای صورت می گیرد که به یک قطعه ساده برای مثال یک شمشال، میان دو یا تعداد بیشتری از اجزای قالب، اعمال نیرو شود تا در اثر تغییر شکل پلاستیک فرم نهایی حاصل شود. فرآیندهای آهنگری معمولا دور ریز خیلی کمی دارند و مدت زمان خیلی کمی برای رسیدن به قطعه نهایی صرف می کنند. بنابراین استفاده از این فرآیند موجب صرفه جویی در هزینه و مواد اولیه می شود، به خصوص در تولیدات انبوه که هزینه استهلاک قطعات نیز به طور تصاعدی بالا می رود. از سوی دیگر، قطعاتی که طی فرآیند آهنگری تولید شده اند معمولا خواص مکانیکی و متالورژیکی بهتری نسبت به فرآیندهای ماشین کاری و ریخته گری دارند.
فورجینگ بسته به دمای فرآیند، روش طراحی و ساخت قالب فورج و فرم قطعه نهایی طبقه بندی های گوناگونی دارد که در ادامه به اختصار شرح داده می شوند. فورجینگ داغ به فرآیندی اطلاق می شود که دمای فرآیند به 75 درصد دمای ذوب آلیاژ برسد یا به عبارت بهتر، از دمای تخریب خواص متالورژیکی آلیاژ گذر نکند. انتخاب بین دمای فورجینگ اغلب با توجه به ملاحظاتی در خصوص هزینه، جنس قطعه کار و کیفیت مد نظر قطعه نهایی صورت می گیرد. ساخت قالب فورج در این فرآیند به گونه ای صورت می گیرد که مقاومت خوبی در برابر خرابی های ناشی از حرارت داشته باشد. فورجینگ داغ در موارد زیر استفاده می شود: 1-بار مورد نیاز برای فورجینگ ماده سازنده آنقدر بالا باشد که تجهیزات و ابزار موجود برای ساخت قالب فورج توان انجام این کار را نداشته باشند. برای مثال ماده ای با استحکام و تنش سیلان بالا یا ابعاد بسیار زیاد که تکنولوژی موجود برای طراحی قالب فورج مناسب برای این منظور کافی نباشد. 2-کارسختی قطعه بعد از اعمال تغییر شکل سرد مطلوب نباشد و قطعه نهایی برای استفاده نیاز به فرآیند های آنیل متعدد داشته باشد. فورجینگ داغ بسته به روش ساخت قالب فورج و نوع فرآیند مدنظر تنوع بسیاری دارد. پر کاربرد ترین آنها فورج قالب بسته و فورج قالب باز هستند. باقی فرآیندهای آهنگری داغ نیز در ادامه به اختصار شرح داده شده اند. در این فرآیند، فلز داغ در دیواره یا حفره ای درون دو سر قالب قرار می گیرد و دو سر قالب تماما دور تا دور قطعه را در بر می گیرند. ساخت قالب فورج ممکن است به گونه ای باشد که حفره یاد شده تماما در یکی از سرهای قالب ایجاد شود یا بین دو سر قالب تقسیم شود. در کنار محفظه اصلی دو راهگاه و حفره کوچیکتر برای کنترل اضافه ماده و کمک به پر شدگی کامل قالب ایجاد می شوند و در کنار قطعه فورج شده ایجاد فلش (Flash) یا پلیسه می کنند. تصویر زیر شماتیک قالب فورج بسته را به تصویر می کشد. با وجود بالاتربودن قیمت ساخت قالب فورج بسته نسبت به قالب فورج باز، قالب بسته دقت ابعادی زیاد و نیاز به ماشین کاری ثانویه کمتری دارد. قطعاتی تا وزن چند تن قابلیت فورجینگ توسط این فرآیند را دارند. فرآیند فورجینگ داغ که در آن فلز بوسیله چکش های تخت فشار بخار یا پرس هیدرولیک بین دو قالب صاف یا شکل دار فرم داده می شود. در این فرآیند محدودیت ابعادی و وزنی چندانی وجود ندارد. قطعاتی به طول 23 متر و وزن ششصد تن توسط این فرآیند فورج شده اند. فورجینگ با قالب باز در این موارد انجام می شود. 1-قطعه تحت فورج قرار گرفته به حدی بزرگ باشد که توسط فورجینگ با قالب بسته قابل انجام نباشد. 2-حجم تولید به قدری محدود باشد که صرف هزینه برای ساخت قالب فورج بسته منطقی نباشد. 3-ارضای الزامات مورد نیاز در خصوص خواص مکانیکی قطعه تنها تحت این فرآیند ممکن باشد. قالب های متفاوت فرآيند فورجینگ در قالب باز در تصویر زیر ترسیم شده اند. ساخت قالب فورج به شیوه a منجر به تولید دیسک های صاف می شود می شود. با تعبیه حفره های v شکل یا چند ضلعی می توان به دیسک های با سطح مقطع گوناگون دست یافت. ساخت قالب فورج برای انجام فرآیند های b،c و d به ترتیب به منظور نازک کردن سطح مقطع شمشال ها، لوله ها و حلقه ها انجام می شود. سرکوبی داغ به عمل زیاد کردن قطر یا تغییر دادن شکل یک میله در انتها، یا در قسمت میانی، به وسیله اعمال فشار و دما در جهت طول آن گفته می شود. قالب های این فرآیند فورجینگ اغلب از دو قسمت یا بیشتر تشکیل شده و هر سری قالب دارای چند محفظه برای مراحل مختلف تغییر شکل است. تصویر زیر چند نمونه از ساخت قالب سرکوبی را به تصویر می کشد. کاهش ضخامت و ازدیاد طول میله های گرد یا مستطیل شکل به روش فورجینگ غلتکی صورت می گیرد. ساخت قالب فورج به این روش بمنظور تهیه میله های با قطع متغیر و فنر های تیغه ای انجام می شود. در ساخت قالب فورج برای دستگاه فورجینگ غلتکی از دو غلتک نیمه استوانه ای استفاده می شود که شیارهایی با مقاطع مورد نظر و کمی خارج از مرکز نسبت به محور چرخش بر روی آن ها ایجاد شده است. میله گداخته را هنگامی که غلتک ها باز هستند، در دهانه بین آنها قرار می دهند. در باقی موارد فورجینگ (به جز دو مورد ذکر شده در فورجینگ داغ) به دلیل پایین تر بودن قیمت ساخت قالب فورج سرد و کمتر بودن هزینه های این فرآیند ترجیحا از فورجینگ سرد می شود. فورجینگ سرد مزایایی نیز از جمله دقت ابعادی بالاتر به دلیل نبود اعوجاج و انقباض حرارتی و کیفیت سطح بیشتر به دلیل تشکیل نشدن پوسته اکسیدی روی سطح قطعه کار دارد. از میان فرآیند های فورجینگ سرد می توان به اکستروژن (extrusion) رو به جلو (جهت حرکت ماده در جهت حرکت سنبه) و اکستروژن رو به عقب (جهت حرکت ماده خلاف حهت سنبه) اشاره کرد. این دو فرآیند در تصویر ترسیم شده اند. مهمترین علت خرابی در ساخت قالب فورج سایش است. سایش قالب در نتیجه لغزش قالب و قطعه کار نسبت به یکدیگر و اصطکاک بین این دو رخ می دهد. سایش قالب در دراز مدت موجب کاهش دقت ابعادی قالب می شود و در نهایت تغییرات ابعادی به حدی می رسد که تعویض قالب ضروری می گردد. دومین دلیل عمده خرابی قالب ها شکست خستگی است. خستگی در نتیجه چرخه تنش های مداومی رخ می دهد که به قالب وارد می شود. خستگی در نواحی تمرکز تنش، برای مثال زوایای تند، تسریع می شود. حفره های ماده، شیارها، راهگاه های پلیسه از جمله عناصری در طراحی قالب فورج است که می توانند به دلیل داشتن زاویه های تند منشا ترک های خستگی باشند. سومین دلیل عمده خرابی قالب تغییر شکل پلاستیک است. تغییر شکل پلاستیک وقتی رخ می دهد که تنشهای وارد شده به قالب از حد تسلیم گذر کند. در این صورت اعوجاج زیاد یا تغییرات شدید ابعاد اولیه ساخت قالب فورج می تواند منشا تخریب قالب یا تغییرات دقت ابعادی قطعات تولیدی باشد. تصویر بالا شماتیک چهار نمونه خرابی در طراحی قالب فورج بسته را ترسیم می کند. انتخاب مواد اولیه برای ساخت قالب فورج تا حد زیادی بستگی به دمای انجام فرآیند فورجینگ ، بار اعمال شده و نحوه سرد کردن قالب دارند. فولادهای ابزار دارای کروم (سری های H10-H14) پر استفاده ترین فولادهای مورد استفاده در ساخت قالب فورج داغ هستند. قالب های استفاده شده از این نوع فولاد سختی خود را تا دمای 425 درجه سانتیگراد حفظ می کنند. فولادهای ابزار دارای تنگستن (سری H21-26) سختی خود را تا 620 درجه سانتیگراد حفظ می کنند، اما مقاومت خوبی در برابر شوک حرارتی ندارند و بنابراین قابلیت سرد شدن بوسیله آب را ندارند. خواص فولادهای ابزار دارای مولیبدن بین این دو نوع فولاد قرار می گیرد و اضافه کردن وانادیم به این فولاد مقاومت به سایش و خستگی حرارتی را افزایش می دهد. فولادهای رسوب سختی از جمله 6F4 نیز این توانایی منحصر به فرد را دارند، که در ابتدای فرآیند با انتقال گرما از قطعه پیش گرم شده سخت تر می شوند و مقاومت به سایش بیشتری را می پذیرند. به طور کلی موادی که به منظور طراحی قالب فورج داغ استفاده می شوند، بایستی توانایی های زیر را داشته باشند. فولادهای مورد استفاده در ساخت قالب فورج بایستی عمق سختی پذیری بالا و مقاومت در برابر نرم شدگی در دمای فرآیند داشته باشند. سختی فولادهایی مانند H11 بعد از نگه داری به مدت 30 دقیقه در دمای حدود 600 درجه سانتیگراد به نصف کاهش می یابد. سایش در دراز مدت موجب تغییر ابعاد یا شکل قالب می شود. مقاومت به سایش اغلب رابطه مستقیم با سختی فولاد دارد. در نتیجه فولادی که سختی و مقاومت به نرم شدگی در دمای بالای بیشتری داشته باشد، از لحاظ مقاومت به سایش نیز کارکرد خوبی در دمای بالا خواهد داشت. با افزایش دمای فرآیند، استحکام تسلیم فولاد کاهش خواهد یافت و فولاد به راحتی دچار تغییر شکل پلاستیک و اعوجاج دائمی می شود. معمولا بین استحکام تسلیم در دمای بالا و مقاومت در برابر نرم شدگی رابطه مستقیمی وجود دارد. چقرمگی عبارت است از قابلیت ماده برای جذب انرژی بدون اینکه دچار شکست بشود. چقرمگی عامل مهمی برای جلوگیری از شکست ترد است و با افزایش دما افزایش خواهد یافت. بنابراین بهتر است که ماده اولیه قالب به گونه ای انتخاب شود که در دمای فرآیند مقاومت خوبی در برابر شکست داشته باشد. چقرمگی رابطه معکوس با سختی دارد؛ در نتیجه فولاد هایی که سختی کمتری دارند (از جمله فولادهای دارای کروم) به این منظور مناسب تر هستند. به طور کلی انتخاب ماده اولیه برای ساخت قالب فورج هنر ایجاد تعادل بین دو خاصیت مکانیکی سختی و چقرمگی و تعیین اهمیت هر کدام از این دو است. انبساط ناهمگن که متاثر از اختلاف شدید دمایی از سطح تا مرکز قالب است، عامل اصلی بروز ترک های ناشی از خستگی حرارتی است. بنابراین ماده ای که ضریب انتقال گرمای بیشتر و انبساط حرارتی کمتری داشته باشد، تفاوت دمای قالب توجهی از سطح تا عمق ندارد، دچار تنش های انبساطی/انقباضی نیست و آسیب پذیری کمتری در برابر این نوع خستگی دارد. از این نظر فولاد H10 نسبت به سایر فولادهای هم رده، مقاومت بهتری در برابر این نوع ترک دارد و برای ساخت قالب فورج مقاوم در برابر خستگی حرارتی استفاده می شود. مقاومت در برابر خستگی مکانیکی بیشتر وابسته به طراحی قالب فورج است. هر چند با برخی عملیات سطحی می توان ماده اولیه را نسبت به خستگی مقاوم کرد. نیترایدینگ سطح، ساچمه زنی و پالیش کردن می توانند شروع ترک های خستگی را به تعویق بیندازند. نکته مهم دیگر این است که انواع آبکاری از جمله آبکاری کروم، نیکل و روی موجب تسریع فرآیند خرابی قالب به دلیل خستگی خواهند شد. قیمت ساخت قالب فورج به مواد اولیه استفاده شده برای ساخت آن بستگی دارد. این مواد اولیه به دو دستی مواد اولیه آهنی و غیر آهنی تقسیم می شوند. استفاده از مواد اولیه به منظور ساخت قالب فورج تا حد زیادی بستگی به نوع فرآیند و هندسه ابزار دارد. در اکستروژن رو به جلو مقاومت ماده در برابر تنش های فشاری اهمیت دارد، اما در اکستروژن رو به عقب مقاومت در برابر سایش خراشان نیز اهمیت دارد. به طور کلی در طراحی قالب فورج سرد انتخاب مواد از بین فولادها (ازجمله فولادهای کارسخت شده پرآلیاژ و فولادهای کروم دار پر کربن) یا انواع کاربید (به خصوص کاربید تنگستن) صورت می گیرد. جدول بالا برخی از آلیاژهای فولاد مورد استفاده در ساخت قالب فورج را بر اساس پارامترهای یاد شده مرتب می کند. سوپر آلیاژهای پایه نیکل و کبالت خواص بسیار بهتر و دمای عملکرد به مراتب بالاتری نسبت به فولادها دارند. رسوب سختی سوپرآلیاژ باعث می شود تا سوپر آلیاژ های پایه نیکل تا دمای 1200 درجه سانتیگراد قابل استفاده باشند. اما بالاتر بودن قیمت ساخت قالب فورج ساخته شده با این آلیاژها استفاده از آن ها را، به جز برای موارد خاص، از نظر اقتصادی محدود می کند. از میان مواد دیگر قابل استفاده برای ساخت قالب فورج می توان به سرامیک ها اشاره کرد. عمر قالب های فورجینگ ساخته شده از سرامیک ها دو برابر قالب های ساخته شده از فولادها است. هر چند قیمت ساخت قالب فورج ساخته شده از این مواد بسیار بالا خواهد بود. استفاده از کاربید ها قیمت ساخت قالب فورج را بالاتر می برد اما مقاومت به سایش به مراتب بهتری دارند. چنانچه هر کدام از ابزار قالب تحت تنش کششی قرار بگیرند، کاربید ها انتخاب نامناسبی برای آن ابزار خواهند بود. از سوی دیگر اگر تنش فشاری وارد بر ابزار بیشتر از 2500 مگاپاسکال تخمین زده شود، استفاده از کاربید لازم می شود. انتخاب بین این دو ماده ملاحظات بسیار دیگری نیز دارد که در منابع مختلف به آن ها اشاره شده است.ساخت قالب فورج برای فورجینگ داغ
ساخت قالب فورج برای فورجینگ در قالب بسته
ساخت قالب فورج برای فورجینگ در قالب باز
سرکوبی یا پرچ کاری داغ
فورجینگ غلتکی
ساخت قالب فورج برای فورجینگ سرد
مهمترین علل خرابی مربوط به ساخت قالب فورج
مواد مورد استفاده برای ساخت قالب فورج داغ
قابلیت سختی پذیری بالا
مقاومت در برابر سایش
مقاومت در برابر تغییر شکل پلاستیک
چقرمگی
مقاومت در برابر خستگی حرارتی
مقاومت در برابر خستگی مکانیکی
قیمت ساخت قالب فورج
مواد اولیه آهنی قالب فورج
مواد اولیه غیرآهنی قالب فورج
فرمت یک راه حل نوین جهت رفع نیازهای صنعتی است. هدف فرمت ایجاد بستری برای معرفی، بررسی و مقایسه ی خدمات صنعتی ارائه شده توسط ارائه دهندگان مختلف و انتخاب بهترین راه حل جهت رفع مشکلات و پاسخگویی به نیازهای صنایع مختلف است.
آدرس: تهران، خیابان آزادی، دانشگاه صنعتی شریف
ایمیل: info@formmat.ir