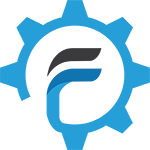
فرمت
محل ارائه خدمت: تهران
شماره تماس: 02191303797
فرمت » ساخت قطعات فلزی » قالب سازی » ساخت قالب خمش
تعداد ارائه دهندگان:
محل ارائه خدمت: تهران
شماره تماس:
[UAS_loggedin]
مشاهده
محل ارائه خدمت: مشهد
شماره تماس:
[UAS_loggedin]
مشاهده
محل ارائه خدمت: تهران
شماره تماس:
[UAS_loggedin]
مشاهده
محل ارائه خدمت: تبریز
شماره تماس:
[UAS_loggedin]
مشاهده
محل ارائه خدمت: مشهد
شماره تماس:
[UAS_loggedin]
مشاهده
محل ارائه خدمت: تهران
شماره تماس:
[UAS_loggedin]
مشاهده
یکی از فرآیندهای متداول شکل دهی ورق های فلزی، خمکاری ورق می باشد. ساخت قالب خمش باید به گونه ای انجام شود که موجب کرنش یکنواخت ورق فلزی حول محوری خطی از 1 تا 180 درجه شود.
ساخت قالب خمش به اشکال متفاوتی انجام می شود که همگی شامل یک یا تعداد بیشتری سنبه و ماتریس منطبق بر هم هستند. این قالب بر سر دستگاهی سوار می شود که به آن ماشین پرس بریک (Press Brake) گفته می شود. در این دستگاه ها سنبه بر سر ابزاری به نام رام (Ram) یا فک بالایی سوار می شود که وظیفه انتقال نیرو به ورق را دارند. انتقال نیرو در رام به سه روش مکانیکی، هیدرولیکی و پنوماتیکی انجام می شود. دستگاه های مکانیکی هزینه کمتر ولی دقت پایینتر و سرعت و بازدهی کمتری نسبت به انواع دیگر پرس بریک دارند. ماتریس در این دستگاه ها روی تخت یا فک پایینی نصب می شود و بسته به نوع دستگاه می تواند ثابت یا متحرک باشد. تصویر زیر نمونه دستگاه پرس بریک هیدرولیکی را به تصویر می کشد. طراحی قالب خمش با توجه به امکانات این دستگاه صورت می گیرد.
قالب های خمش انواع گوناگونی دارند. ساخت قالب خمش و انتخاب نوع آن با توجه به نیازهای کیفی قطعه نهایی یا محدوده هزینه ساخت قالب خمش تعیین می شود. در ادامه چند نمونه انواع قالب های خمش به طور خلاصه شرح داده شده اند. قالب خمش V شکل پرکاربرد ترین نوع قالب خمش است. در ساخت قالب خمش به این روش از یک سنبه و یک ماتریس با حفره ای V شکل استفاده می شود تا ورق ها به شکل زاویه حفره درون ماتریس خم شوند. طی این فرآیند سنبه روی ورق فلزی اعمال نیرو کرده و ورق با حرکت به درون حفره V شکل ماتریس دچار تغییر شکل پلاستیک می شود. تصویر زیر مکانیسم کلی قالب های V شکل را به تصویر می کشد. نوع ساخت قالب خمش در این فرآیند با توجه به شکل سنبه و ماتریس به دسته های زیر تقسیم می شود. سکه زنی به روشی اطلاق می شود که به دلیل دقت ابعادی بالا به طور گسترده ای استفاده می شود. طی این روش از نیرو و فشاری تا سی برابر روش های دیگر خمش استفاده می شود. در ساخت قالب خمش برای فرآیند سکه زنی، سنبه و ماتریس کاملا از نظر فیزیکی چفت بوده و نیروی وارد شده موجب نازک تر شدن نوک خم ورق می شود. در این روش برگشت فنری وجود ندارد. تصویر زیر شماتیک فرآیند سکه زنی را نشان می دهد. در این روش، همانطور که مشخص است، ورق فلزی تا کف حفره ماتریس فشرده شده تا به طور دقیق زاویه و شکل حفره را به خود بگیرد. در این نوع ساخت قالب خمش ، مکان و شکل حفره V شکل نتیجه خمش را مشخص می کند. تصویر زیر شماتیک فرآیند خمش کفی را به تصویر می کشد. این روش ساخت قالب خمش ، به دلیل سادگی انجام فرآیند و عدم نیاز به نیروی زیاد به کار می رود. در این روش خمش که به خمش سه نقطه ای هم شناخته می شود، ورق تنها در سه نقطه با ماتریس تماس دارد و بر خلاف روش های دیگر به کف یا دیواره حفره برخورد نمی کند. بنابراین شکل حفره یا سنبه در فرم نهایی ورق تاثیرگذار نیست و فرم نهایی تنها توسط نیروی وارده دیکته می شود. در این روش برگشت فنری بیشتر از دو روش دیگر است و در هنگام شکل دهی تاثیر تغییرات زاویه ناشی از برگشت نیز باید لحاظ کرد. تصویر زیر شماتیک این فرآیند را ترسیم می کند. یکی دیگر از روش های ساخت قالب خمش ورق که از سه بخش سنبه، ورقگیر و ماتریس تشکیل شده است. ورق بین ورقگیر و ماتریس محکم شده و بخشی که خارج از ورقگیر می ماند توسط فشار سنبه خم می شود. در این روش توان ایجاد زوایای بیش از 90 درجه وجود ندارد و طراحی مناسب به منظور حذف اثر برگشت فنری نیاز به آزمون و خطا دارد. این روش شباهت زیادی به قالب خمش V دارد، با این تفاوت که حفره درون ماتریس شکلی مشابه با حرف U دارد. در این روش بعد از اعمال فشار توسط سنبه، به دلیل برگشت فنری قطعه به حفره می چسبد و بنابراین نیاز به بیرون انداز وجود دارد. تصویر زیر شماتیک ساخت قالب خمش به شکل U را ترسیم می کند. در فرآیند خمش چرخشی از حرکت دورانی سنبه برای خمش ورق استفاده می شود. مزیت بزرگ این روش نسبت به روش های خمش L شکل و V شکل سایش کمتر ابزار و ورق در این فرآیند است. با استفاده از سنبه های پلیمری حتی کوچکترین نشانی نیز از سایش حین فرآیند روی سطح قطعه کار نمی ماند و قطعه کار سطحی کاملا تمیز خواهد داشت. در این روش امکان ایجاد زوایای بالای 90 درجه نیز وجود دارد. در ضمن برگشت فنری نیز در این روش کمتر از روش های خمش L شکل و V شکل است. فرآیند دایره ای کردن به منظور فرم دهی لبه های ورق به شکل دایره های توخالی انجام می شود. هدف از این کار حذف لبه های تیز و افزایش ممان اینرسی نواحی گرد شده است. نمونه ای از اشکال گوناگون قالب های گردزنی به همراه ورقی با لبه های دایره ای شده در تصویر زیر ترسیم شده است. ساخت قالب خمش در این فرآیند به صورت دو مرحله ای انجام می شود تا شکل دایره ای به طور کامل حاصل شود. فرآیند لبه زنی همانند فرآیند دایره ای کردن روی لبه های ورق انجام می شود. با این تفاوت که در فرآیند لبه زنی، لبه ورق روی خود تا می شود. این فرآیند در دو مرحله انجام می شود که در مرحله اول خمی با زاویه 30 تا 45 درجه در لبه ورق ایجاد شده و در ادامه بوسیله فشار سنبه لبه خم بسته می شود. لبه زنی نیز مثل دایره زنی به دلیل استحکام دادن به لبه ورق و حذف لبه های تیز انجام می شود. تصویر زیر نمونه ای از ساخت قالب خمش را به منظور لبه زنی به تصویر می کشد. از فرآیند خمش با غلتک برای خم کردن ورق فلزی به شکل لوله یا اشکال منحنی استفاده می کنند. در ساخت قالب خمش برای این فرآیند از یک دستگاه پرس هیدرولیک و دسته های سه تایی غلتک به منظور ایجاد یک خم بزرگ یا خم های متعدد در ورق استفاده می شود. تصویر زیر شماتیکی از قالب خمش با غلتک را به تصویر می کشد. پدیده برگشت فنری، بیانگر تغییر شکل ورق، پس از بار برداری و رها شدن از نیروی پرس، در فرآیند خمش می باشد. بنابراین در فرم دهی قطعه کار معمولا این برگشت لحاظ شده و خمش تا زاویه ای بیشتر از زاویه طراحی انجام می شود. این پدیده دستیابی به دقت ابعادی مورد نظر را سخت می سازد و باعث می شود مونتاژ قطعه با مشکلات پیش بینی نشده ای مواجه گردد. یک بررسی اقتصادی نشان می دهد که صنعت خودروسازی آمریکا سالانه 50 میلیون دلار به خاطر پیامدهای کیفی پدیده برگشت فنری متضرر می شود. بنابراین لحاظ کردن برگشت فنری در ساخت قالب خمش از اهمیت بالایی برخوردار است. این پدیده به دلیل ناهمگنی تنش ها در راستای عرض قطعه خم شده رخ می دهد. همانطور که در تصویر زیر قابل مشاهده است، ورق تحت خمش در بخش های داخلی تحت فشار و در بخش های خارجی تحت کشش قرار می گیرد. تنش وارد شده به قطعه در خطی در مرکز قطعه کار صفر است که به آن خط محور خنثی می گویند. برآیند تنشهای پسماند فشاری و کششی موجب تلاش قطعه کار برای برگشت به حالت اول و تغییر زاویه آن می شود. تصویر زیر شماتیک تنش های اعمال شده به قطعه خمش شده را ترسیم می کند. اثر برگشت فنری برای موادی که استحکام تسلیم بیشتری دارند، قوی تر است. فولادهای زنگ نزن به مراتب بیشتر از آلومینیوم، مس یا فولادهای کم آلیاژ معمولی مستعد برگشت فنری هستند. کاهش زاویه و ابعاد ورودی حفره دو عاملی هستند که موجب کم شدن اثر برگشت فنری می شوند. با افزایش ضخامت قطعه کار نیز برگشت فنری کمتر می شود. انتخاب مواد اولیه برای ساخت قالب خمش به منظور استفاده در دستگاه پرس بریک تا حد زیادی بستگی به جنس و شکل قطعه کار، شدت فرم دهی مدنظر و حجم تولید دارد. به منظور تغییر شکل های ساده در ماتریس های V شکل اغلب از فولادهای ساده کربنی یا آهن خاکستری استفاده می شود که هزینه پایین و عمر قابل قبولی در استفاده های سبک دارند. همچنین در خمش هایی که نیاز به نیروی بیشتر دارند یا در حجم های تولید بالاتر، استفاده از فولادهای سختی پذیر به همراه سخت کاری شعله ای نوک سنبه و لبه های ماتریس V شکل توصیه می شود. در خمش های سنگین تر که نیاز به ابزاری با استحکام و مقاومت به سایش بیشتر دارند و نیروی بیشتری به سطح قطعه اعمال می کنند، طیف وسیعی از مواد اولیه قابل استفاده هستند. طیف وسیعی که شامل آلیاژهای آهنی مثل چدن ها و فولادهای ابزار و کاربیدها و سرامیک های خاص می شود. یورتان (تصویر بالا) که پلاستیکی بسیار مستحکم است، یکی از جدیدترین مواد مورد استفاده در ساخت قالب خمش می باشد و توسط روش هایی مثل پرینت سه بعدی یا تزریق پلاستیک به شکل قالب در می آید. پارامترهای متعددی تعیین کننده هزینه ساخت قالب خمش هستند. ابعاد قطعه هر چه بیشتر باشند، طول سنبه و ماتریسی که باید روی دستگاه پرس بریک نصب شوند بیشتر می شود. ضخامت ورق، عمق کشش، تیراژ تولید و جنس قطعه تعیین کننده نیروی لازم برای انجام خمش و استهلاک ابزار است و با افزایش نیرو برای ساخت قالب خمش به مواد اولیه گران تری باید روی آورد. همچنین نوع فرآیند و پیچیدگی های طراحی قطعه تعیین کننده تعداد قالب های مورد نیاز برای رسیدن به فرم نهایی قطعه هستند.انواع قالب های خمش
ساخت قالب خمش V شکل
ساخت قالب خمش V شکل برای انجام فرآیند سکه زنی (Coining)
ساخت قالب خمش V شکل برای انجام فرآیند تماس با کف (Bottoming)
ساخت قالب خمش V شکل به روش هوایی (Air Bending)
ساخت قالب خمش L شکل
ساخت قالب خمش U شکل
ساخت قالب خمش برای انجام فرآیند خمش چرخشی (Rotary bending)
فرآیند Curling یا دایره ای کردن لبه های ورق (قالب گردزنی)
فرآیند لبه زنی یا Hemming (قالبهای لبه زنی)
فرآیند خمش با غلتک یا Roll Bending
برگشت فنری
انتخاب مواد اولیه برای ساخت قالب خمش
هزینه ساخت قالب خمش
فرمت یک راه حل نوین جهت رفع نیازهای صنعتی است. هدف فرمت ایجاد بستری برای معرفی، بررسی و مقایسه ی خدمات صنعتی ارائه شده توسط ارائه دهندگان مختلف و انتخاب بهترین راه حل جهت رفع مشکلات و پاسخگویی به نیازهای صنایع مختلف است.
آدرس: تهران، خیابان آزادی، دانشگاه صنعتی شریف
ایمیل: info@formmat.ir