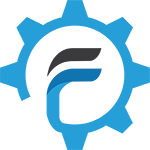
فرمت
محل ارائه خدمت: تهران
شماره تماس: 02191303797
فرمت » ساخت قطعات فلزی » برشکاری » برش حرارتی » برش پلاسما
تعداد ارائه دهندگان:
محل ارائه خدمت: کرج
شماره تماس:
[UAS_loggedin]
مشاهده
محل ارائه خدمت: تهران
شماره تماس:
[UAS_loggedin]
مشاهده
در فرآیند برش پلاسما از جریان پر سرعت گاز نجیب یا هوای فشرده شده استفاده می شود که از یک نازل عبور داده می شود. همزمان با دمش گاز ، بین سطح قطعه کار و نازل یک قوس الکتریکی (نازل نقش کاتد و قطعه آند) ایجاد می شود. در نتیجه گاز یونیزه شده و به حالت پلاسما در می آید. وظیفه گاز یونیزه شده یا پلاسما انتقال الکتریسیته و گرما دادن از مشعل دستگاه پلاسما برش به قطعه کار است. این گرما به اندازه ای است که موجب ذوب شدن قطعه کار شود. سرعت بالای جریان گاز حین بعد از انجام فرآیند ذوب شدن ماده، موجب پراکندگی و خارج شدن ماده مذاب از محل برش پلاسما می شود.
ماهیت فیزیکی ماده (جامد، مایع و گاز) توسط گرمایش قابل تغییر است. با افزایش انرژی گرمایی در ماده حرکت بی نظمی اتم ها افزایش یافته و ماده به ترتیب از شکل منظم جامد به مایع و سپس به گاز تبدیل خواهد شد. با جذب انرژی گرمایی بیشتر توسط گاز برخی خصوصیات فیزیکی آن از قبیل انتقال الکتریسیته دچار تغییر می شود. این فرآیند یونیزاسیون نامیده می شود و مبنای برش پلاسما است. در حالت پلاسما گاز یونیزه می شود. به این معنی که فضایی از یون ها و الکترون ها در میان اتم های گاز ایجاد خواهد شد و منجر به رسانایی گاز می شود. برش پلاسما به وسیله گذراندن این جریان از یک روزنه تنگ کننده انجام می شود. در این شرایط جریان بسیار متراکم شده و قابلیت ذوب قطعه کار را دارد. دستگاه های پلاسما برش به منظور شروع قوس از چند روش استفاده می کنند. در روش فرکانس بالا یا HF یک جرقه با ولتاژ بالا موجب یونیزاسیون گاز شده و فرآیند برش پلاسما شروع می شود. این روش دارای خطراتی از جمله برق گرفتگی و تشعشعات رادیویی است. در فرآیند دیگر برش پلاسما ، نوک مشعل به طور لحظه ای به قطعه کار برخورد کرده و فاصله می گیرد. این برخورد باعث ایجاد یک مدار بسته و شروع جریان می شود. در این روش مشعل دارای یک کلاهک ضد ضربه است. معمول ترین روش آغاز قوس، ایجاد قوس اولیه بین الکترود و نازل است. فرآیند برش پلاسما به طور معمول در چند مرحله انجام می شود. در ابتدا الکترود به منبع برقی متصل می شود که به آن ولتاژ منفی قوی اعمال می کند. دمش گاز در مشعل آغاز شده و همزمان گاز در حال دمش گردش می کند. نازل به قطب مثبت ژنراتور وصل می شود و یک پتانسیل با ولتاژ و فرکانس بالا بین الکترود و نازل اعمال می شود. این پتانسیل تولید قوس کوچکی بین نازل و الکترود می کند که موجب یونیزه شدن گاز در حال دمش می شود. یونیزه شدن گاز موجب شروع قوسی بزرگ تر بین الکترود و نازل شده که به آن قوس پیلوت گفته می شود. قوس پیلوت به وسیله دمش گاز به سمت خارج از نازل هدایت شده و در نهایت با قطعه کار تماس پیدا می کند. تماس قوس پیلوت با قطعه کار موجب برقراری قوس اصلی می شود. نازل از جریان خارج می شود و الکترود به قطب مثبت تبدیل می شود. در نهایت قوسی قدرتمند با دمای بسیار بالا ایجاد می شود که آغازگر برش پلاسما است. جریان پلاسمایی که با این روش ها تولید می شود، دمایی حدود 25 هزار درجه سانتی گراد دارد و سرعت آن به سرعت صوت می رسد. در موارد معدودی در برش پلاسما امکان دارد که نازل از مدار بسته خارج نشود که موجب ایجاد قوس دوگانه شود. قوس ابتدایی بین الکترود و نازل در دستگاه باقی می ماند که موجب تخریب و استهلاک نازل می شود. پاشش سرباره به نازل و عدم دقت در زمان اتصال بین نازل و قطعه کار در روش تماسی از عوامل ایجاد قوس دوگانه هستند. نازل در مشعل های برش پلاسما معمولا از آلیاژهای مس ساخته می شود. نازل جریان گاز را تا حد ممکن متمرکز می کند. در مواردی که قوس به صورت تماسی استفاده می شود، به دلیل گرمای بسیار زیاد در نوک نازل از تنگستن استفاده می شود. الکترود استفاده شده برای شروع قوس نیز معمولا از جنس هافنیم یا تنگستن است. تنگستن نیز در برخورد با اکسیژن یا هوای فشرده می سوزد. بنابراین در این موارد از هافنیم استفاده می شود. گاز مورد استفاده در پلاسما برش می تواند اکسیژن، نیتروژن و هوای فشرده یا ترکیبات گرانتر گازهای نجیب باشد. استفاده از اکسیژن کارکردی همانند هوابرش دارد. در برش فولادهای ساده کربنی اکسیژن موجب اکسایش فولاد و سهولت برش می شود. این واکنش سرعت برش پلاسما را افزایش داده و کیفیت لبه را بهبود می بخشد. نیتروژن یا هوای فشرده برای فولاد های زنگ نزن یا آلومینیوم استفاده می شود. در برش موادی که فعال تر هستند، به منظور تمیز بودن سطح برش از آرگون و دیگر گازهای نجیب استفاده می شود. ترکیبات دیگر این گازها با متان یا هیدروژن نیز برای مصارف مختلف کاربرد دارند. به طور تقریبی 30 درصد گاز یونیزه شده و 70 درصد بقیه گاز برای خنک کنندگی و حذف مواد استفاده می شود. گردش گاز نیز یکی از تکنیک های مهم در فرآیند برش پلاسما است. برای مثال، گردش گاز به خنک کنندگی کمک می کند. با گرداندن گاز، اتم های یونیزه نشده سنگین تر و خنک تر به بیرون از ستون گاز در حال گردش کشیده می شوند. در نتیجه لایه ای از هوای سرد حول ستون پلاسما به وجود می آید. هوای سرد از نازل مسی در برابر جریان های بالا محافظت می کند. برش های ضخیم تر نیاز به جریان های بالایی دارند. با بالا رفتن جریان، نسبت اتم های یونیزه شده در گاز بالا می رود و دمای گاز بیشتر می شود. در نتیجه، نازل مسی به سرعت تخریب و مستهلک می شود. در جریان های بالای برش پلاسما ، گردش گاز از اهمیت بیشتری برخوردار می شود. بدون گردش قوس، تعادل دمایی در ستون قوس نامتوازن بوده و جفت سطوح برش پلاسما دچار پخ می شوند. در مواردی پخ به اندازه ای است که قطعه کار بعد از اتمام پلاسما برش بلااستفاده می شود. گردش قوس باعث می شود که یک سمت برش کاملا عمود بر قطعه کار انجام شود. با تغییر جهت گردش قوس، سطح برش دارای پخ تغییر می کند. دمش گاز محافظ در برش پلاسما نیز می تواند به تنگ کردن قوس و خنک کنندگی نازل کمک کند. دمش گاز بعد از شروع فرآیند تشکیل پلاسما و یونیزاسیون انجام می شود. خلوص گاز نیز از اهمیت زیادی برخوردار است. حداقل خلوص مورد نیاز در پلاسما برش برای نیتروژن 99.995 درصد و برای اکسیژن 99.5 درصد است. اگر خلوص زیر موارد گفته شده باشد، احتمال دارد که عمر الکترود کاهش یابد یا قوس نفوذپذیری لازم را نداشته باشد یا سطح کار را آلوده کند. برش پلاسما از لحاظ طیف مواد قابل برش انعطاف پذیری بیشتری نسبت به هوابرش دارد. برش پلاسما همانند برش وایرکات برای انواع مواد رسانا از قبیل فولادهای کم کربن، فولاد زنگ نزن، آلومینیوم، انواع برنج ها و تیتانیوم قابل استفاده است. اما هوابرش به این دلیل که وابسته به نقطه ذوب اکسید ماده قطعه کار است، محدود به آلیاژهای آهنی می شود. در برش فولادهای زنگ نزن و آلومینیوم به دلیل نسوز بودن اکسیدها از روش پلاسما برش استفاده می شود. مهمترین معایب برش پلاسما مربوط به حفظ ایمنی و سلامت اپراتور ها است. صدای تولید شده توسط برش پلاسما بین 90 تا 120 دسی بل و در حد آستانه دردناکی برای گوش انسان است. جریان برش پلاسما نیز بین 100 تا 800 آمپر است و تولید نور شدیدی می کند که بدون عینک قابلیت از بین بردن توان بینایی را دارد. اپراتور های پلاسما برش بایستی مجهز به گوش گیرها و محافظ های بینایی مناسب برای جلوگیری از آسیب دیدگی باشند. همچنین از بین معایب برش پلاسما می توان به ایجاد گازهای سمی اشاره کرد. برای نمونه کروم هگزاوالان یکی از گازهای سمی ایجاد شده حین برش فولادهای زنگ نزن است که موجب سرطان می شود. برای افزایش ایمنی اپراتورها و رفع معایب برش پلاسما در بحث ایمنی نیاز است که سیستم های مکش هوای قوی مانع از انتشار این گازها به محیط شوند. برخی از معایب برش پلاسما روی کیفیت برش و قطعه کار مطرح می شوند. برش پلاسما باعث ایجاد منطقه متاثر از حرارت در قطعه کار می شود. در سطح قطعه کار این فرآیند موجب سخت شدن ناحیه برش یا عیوب ریزساختاری دیگر می شود. سطح پلاسما برش معمولا دچار پخ زدگی است. گردش پلاسما توان کم کردن این پخ زدگی را دارد. دقت ابعادی پلاسما برش نیز بیشتر از هوابرش اما بسیار کمتر از برش لیزر فلزات و برش واترجت است. لازم به ذکر است که ابداع روش برش پلاسما در زیر آب موجب رفع اغلب معایب برش پلاسما به خصوص در رابطه با صدا، نور، گازهای سمی و تاثیر حرارت شده است. از میان دیگر معایب برش پلاسما می توان به کم بودن محدوده ضخامت برش پلاسما اشاره کرد. برش قطعات خیلی نازک با پلاسما برش ، موجب بروز اعوجاج شدید می شود. یکی از راه های جلوگیری از اعوجاج، افزایش تنگ کنندگی نازل و ستون پلاسما به وسیله افزایش دمش گاز محافظ و نازک کردن نوک نازل است. به این منظور که برش حرارت متمرکز تری به قطعه اعمال کند. از سوی دیگر برش زدن قطعاتی با ضخامت بیشتر از2.54 سانتی متر (یا یک اینچ) نیاز به دستگاهی با محدوده شدت جریان بیشتری دارد. قیمت برش پلاسما وابستگی زیادی به ضخامت برش پلاسما دارد. به این دلیل که منابع تغذیه پلاسما استفاده شده شدت جریان و قدرت برش محدودی دارند. دستگاه های ضعیف تر اگر بتوانند چنین قطعه ای را برش بزنند، کیفیتی بسیار پایین را تحویل خواهند داد. دستگاه های قویتر توانایی افزایش ضخامت برش پلاسما تا مقدار تقریبی 15 سانتی متر را دارند. اما چنین برشی با این ضخامت صرفه اقتصادی برای استفاده صنعتی ندارد. سرعت برش نیز عامل تعیین کننده دیگری روی قیمت برش پلاسما است. هر دستگاه بسته به توانایی برش خود، سرعت برش محدودی دارد. در مواردی که نیاز به تولید انبوه وجود دارد یا زمان کافی برای برش وجود ندارد، بایستی از دستگاه های با شدت جریان بالاتر استفاده کرد که موجب بالا رفتن قیمت برش پلاسما می شود. دستگاه هایی که از شدت جربان بالاتری بهره می برند، نسبت به سایر دستگاه ها در ضخامت های مشخص سرعت عملکرد بیشتری دارند. چرخه عملکرد نیز عامل تعیین کننده ای روی قیمت برش پلاسما و دستگاه است. این چرخه محدوده زمانی است که دستگاه می تواند بدون نیاز به خاموش و خنک شدن، برشی مداوم انجام دهد. چرخه عملکرد بالا که نسبت به نوع و جنس دستگاه است، عامل تعیین کننده ای برای سرعت پلاسما برش است. مشعل های برش پلاسما نیز مستهلک می شوند. چنانچه قیمت برش پلاسما پایین در نظر گرفته شده باشد، تعداد قطعات مستهلک شونده افزایش می یابد و عمر مشعل به همان میزان کاهش می یابد. بنابراین با انتخاب مواد اولیه کم کیفیت تر برای دستگاه برش پلاسما و مشعل در کوتاه مدت قیمت برش پلاسما کاهش یافته اما در دراز مدت قیمت های تعمیرات زیاد خواهد شدماهیت پلاسما در برش
فرآیند برش پلاسما
معمول ترین روش انجام فرآیند برش پلاسما
ایجاد قوس دوگانه در فرآیند برش پلاسما
عملکرد مشعل در فرآیند برش پلاسما
گاز در فرآیند برش پلاسما
گردش گاز در پلاسما برش
عملکرد گاز محافظ
خلوص گاز در برش پلاسما
مواد اولیه قابل برش توسط فرآیند برش پلاسما
معایب برش پلاسما
محدوده ضخامت برش پلاسما
قیمت برش پلاسما
فرمت یک راه حل نوین جهت رفع نیازهای صنعتی است. هدف فرمت ایجاد بستری برای معرفی، بررسی و مقایسه ی خدمات صنعتی ارائه شده توسط ارائه دهندگان مختلف و انتخاب بهترین راه حل جهت رفع مشکلات و پاسخگویی به نیازهای صنایع مختلف است.
آدرس: تهران، خیابان آزادی، دانشگاه صنعتی شریف
ایمیل: info@formmat.ir