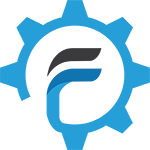
فرمت
محل ارائه خدمت: تهران
شماره تماس: 02191303797
فرمت » ساخت قطعات فلزی » ماشینکاری » فرزکاری و سنگ زنی » سنگ دستی
تعداد ارائه دهندگان:
محل ارائه خدمت: تهران
شماره تماس:
[UAS_loggedin]
مشاهده
محل ارائه خدمت: تهران
شماره تماس:
[UAS_loggedin]
مشاهده
محل ارائه خدمت: تهران
شماره تماس:
[UAS_loggedin]
مشاهده
سنگ زنی جزو دسته فرایندهای براده برداری است و در آن، برداشت مواد توسط اعمال نیروی ذرات خراشان روی قطعه کار، با عمق برداشت کم انجام میشود. دستگاه های سنگزنی قابلیت انجام طیف وسیعی از عملیات سطحی را دارند. بر اساس نوع دستگاه و عملیات سنگزنی انجام شده، نتیجه فرایند می تواند سطح پرداختکاری شده بسیار صاف یا سطح زبر با نرخ برداشت بالای مواد باشد. ذرات خراشان می توانند به صورت ذرات آزاد باشند یا به صورت چسبیده روی یک کمربند به قطعه اعمال شوند. مرسوم ترین فرایند سنگ زنی به شکل چرخ ها یا سنگ های ساینده ای می باشد که در آن، ذرات ساینده توسط ماتریس به یکدیگر چسبیده اند.
سنگ زنی
سایر محصولات استفاده شده برای پرداختکاری و سنگ زنی نیز شامل لایه های کاغذی، پارچه ای یا چرمی می شود. روی این قطعات، به وسیله ترکیبات ساینده و انواع رزین و چسب پوشانده می شود. سپس به شکل های مختلف، به صورت دستی یا مکانیکی، برای پرداختکاری قطعات فلزی و غیر فلزی استفاده می شوند. این دسته محصولات پرداختکاری ، ممکن است یکبار مصرف بوده یا قابلیت چندین مرحله اضافه کردن ذرات ساینده را داشته باشند.
ترکیبات ساینده سنگزنی ، موادی بسیار سخت هستند که برای انجام فرایند سنگ زنی و دیگر عملیات پرداختکاری استفاده می شوند. این ترکیبات همانند دیگر فرایندهای ماشین کاری و تراشکاری براده برداری می کنند اما ابعاد این براده ها بسیار کوچکتر از فرایندهای یاد شده است. مهمترین مشخصه های این ترکیبات شامل سختی بالا، چقرمگی مناسب و مقاومت در برابر فرسایش است.
سختی، تعیین کننده قابلیت نفوذ این ذرات به درون مواد قطعه کار است. هر چه تفاوت سختی بین این ذرات و قطعه کار بیشتر باشد، عمل برداشت مواد و سنگزنی با کارایی بهتری صورت میگیرد. کارایی بهینه ذرات به وسیله شکستن آن ها یا حذف برآمدگی ها و در نتیجه کند شدن آن ها کاهش می یابد. افزایش چقرمگی ذرات، موجب جلوگیری از شکستن و دو نیم شدن ذرات شده و مقاومت به فرسایش، کند شدن آن ها را به تاخیر می اندازد. البته به شکستن ذرات از این دیدگاه نیز می توان نگاه کرد که فرآیند شکستن موجب ایجاد لبه های تیز جدید و بهبود سایندگی آن ها میشود.
آلومینا و کاربید سیلسیم دو ماده پرکاربرد در فرایند سنگ زنی هستند. آلومینا در این بین، بیشترین استفاده را در فرایندهای پرداختکاری و سنگزنی دارد. از آلومینا برای سنگزنی اغلب فولادها، چدن ها و سایر آلیاژهای ریختگی غیرآهنی استفاده می شود. چنانچه آلومینا با اکسیدهای زیرکونیم و تیتانیوم ترکیب شود، نرخ برداشت مواد بالاتر میرود. در هر حال، آلومینا از کاربید سیلیسیم نرمتر است و برای کاربردهای کلی تر استفاده میشود. کاربید سیلیسیم در مقابل، بسیار سخت ولی شکننده است و در سنگ زنی چدنها، مواد غیر آهنی با استحکام پایین و برخی مواد غیر فلزی استفاده می شود.
ترکیبات ابرساینده نیز موادی هستند که در کاربردهای بسیار خاص برای مثال در سنگزنی موادی همچون کاربیدهای سمانته استفاده می شوند. به طور کلی، هزینه سنگ زنی با این مواد بسیار بالاتر می رود. اما از نگاه کارایی و زمان لازم برای انجام فرایند، هزینه سنگ زنی مواد خاص با ترکیبات ابرساینده به صرفه تر است. این ذرات از موادی مانند الماس و نیترید بور مکعبی یا CBN ساخته می شود.
سنگزنی
لازم به ذکر است که استفاده از الماس برای مواد آهنی مناسب نیست. به این دلیل که با افزایش دما در فرایند سنگزنی فولاد با الماس، ماده فولادی از الماس، کربن جذب می کند. طی این فرایند، کربن سطح فولاد افزایش یافته و کارایی ذرات الماسی کمتر می شود. ترکیبات CBN از الماس نرمتر بوده اما در سنگزنی برخی مواد بهتر عمل می کنند، به این دلیل که مقاومت بیشتری نسبت به دمای بالا دارند. به دلیل هزینه بالای این مواد و به منظور کاهش هزینه سنگ زنی ، این ترکیبات تنها در سطح چرخ یا سایر قطعات سنگ دستی متمرکز می شوند.
چرخ سنگزنی از ترکیبات ساینده یا ذرات خراشانی تشکیل میشود که به وسیله ماتریس یا رزین به یکدیگر متصل شده اند. این ذرات هنگامی که چرخ، حرکت دورانی می کند و به قطعه کار اعمال نیرو میکند، مانند دندانه عمل می کنند. خواص عملکردی این چرخ به وسیله نوع و ابعاد ذرات ساینده تشکیل دهنده چرخ تعیین می شود. همچنین تراکم ذرات و نوع و مقدار ماده ماتریس یا رزین ذرات نیز روی عملکرد چرخ موثر است.
ماتریس چرخ سنگ زنی می تواند از نوع ارگانیک یا غیر ارگانیک باشد. ماتریس های ارگانیک می توانند از نوع شیشه ای، سیلیکاتی یا فلزی باشند. ماتریس های شیشه ای یا ویتریفای پر کاربردترین ماده چسباننده برای چرخ های سنگزنی هستند. این ماده از ترکیباتی مثل شیشه سربی یا شیشه بوروسیلیکاتی ساخته می شود که نقطه ذوب پایینی دارد. این ترکیب، پایداری شیمیایی بالایی داشته و در محیط های فعال (برای مثال محیط های خورنده) عملکرد خوبی دارد. به اضافه، این ترکیبات استحکام و صلبیت بالایی دارند، اما در دماهای بالا کاربرد مناسبی ندارند. ترکیبات سیلیکاتی، ترکیبات آب شیشه مستحکم شده به وسیله پخت هستند که برای ساخت چرخ های با ابعاد بزرگ استفاده میشوند. ترکیبات نیترید بور مکعبی و الماسی معمولا در ماتریس های فلزی نگه داری می شوند تا قابلیت انجام پرداختکاری های بسیار سنگین را داشته باشند.
انواع تجهیزات سنگ زنی
چرخ های با ماتریس های ارگانیگ به وسیله موادی از قبیل رزین های فنولی، پلاستیک و شلاک، ذرات را کنار یکدیگر نگه می دارند. این دسته چرخ ها انعطاف پذیر تر از چرخ های غیرارگانیک هستند و ضربه بیشتری را تحمل می کنند. به منظور انجام پرداختکاری های بسیار ظریف می توان از چرخ سنگزنی ارگانیک استفاده کرد.
گرید چرخ سنگ زنی معیاری برای تعیین میزان نگه دارندگی ذرات کنار همدیگر است. ذرات توسط ماتریس نگه دارنده، در جای خود نگه داشته می شوند و اتصال بین ذرات به یکدیگر توسط قابلیت نگه دارندگی ماده ماتریس بیان می شود. سختی چرخ معیار دیگری است که همین مسئله را بیان می کند. میزان این سختی بایستی مقداری متعادل باشد. به این دلیل که چرخ های بسیار سخت، مواد ساینده را حتی بعد از کند شدن، نگه می دارند که موجب کاهش کارایی چرخ می شود. از سوی دیگر در چرخ های بسیار نرم، ذرات پیش از اتمام کارایی از چرخ جدا می شوند. لازم به ذکر است که معیار سختی چرخ با سختی ترکیبات ساینده متفاوت است.
سیستم های پرداختکاری و سنگزنی ، بر اساس شکل چیدمان سیستم، به چندین دسته تقسیم می شوند. فرایندهای سنگ نی تخت و سنگزنی استوانه ای برخی از فرایندهای متداول سنگ زنی هستند.
قطعه کار به شکل قطعاتی با طول و عرض زیاد و ضخامت کم روی صفحه ای قرار میگیرد. این قطعه به وسیله مغناطیس یا نیروی خلا روی صفحه نگه داشته می شود و یک چرخ سنگ زنی به صورت عمودی یا افقی چرخیده و عمل سنگزنی یا پرداختکاری را انجام میدهد. ماشین های سنگ مغناطیسی از این نوع سیستم ها هستند.
سنگ زنی سطوح تخت
در سنگ زنی استوانه ای از چرخ سنگزنی برای پرداختکاری سطوح خارجی غلتک ها، شفت ها و انواع قطعات با سطح مقطع دایره ای استفاده می شود. این ماشین ها به دو نوع مرغک دار یا سنترتایپ و بدون مرغک یا سنترلس تقسیم میشوند.
در ماشین های سنگزنی استوانه ای مرغک دار، قطعه روی دستگاه تراش نصب شده و مرغک، قطعه کار را در موقعیت خود تنظیم می کند. چرخ سنگ زنی با حرکت های محوری و انتقالی عمل برداشت مواد را انجام می دهد.
سنگ زنی استوانه ای مرغک دار
در سنگ زنی استوانه ای سنترلس یا بدون مرغک، قطعه کار توسط مرغک و سه نظام در جای خود نمیچرخد. بلکه از غلتک دیگری به اسم چرخ تنظیم استفاده می شود که قطعه حول محور خود چرخانده شود. سیستم سنترلس بر اساس نوع چرخش قطعه کار و چرخ تنظیم به سه شکل تقسیم می شود.
سنگ زنی استوانه ای سنترلس throughfeed
در سیستم های throughfeed ، چرخ تنظیم به شکلی تنظیم شده که با اندکی انحراف روی قطعه، اعمال نیرو کند و قطعه استوانه ای را در راستای طولی حرکت دهد. این سیستم برای قطعات استوانه ای با طول زیاد جواب میدهد. این نوع تغذیه در صورت وجود هر گونه زائده یا ناهمواری نسبت به شکل دایره ای روی بخشی از میله با مشکل مواجه میشود.
سنگ زنی استوانه ای سنترلس Endfeed و infeed
در سیستمهای infeed ، قطعه بین چرخ تنظیم و چرخ سنگ دستی به گونه ای نگه داشته میشود که حرکت طولی نداشته باشد. در این حالت در صورت ایجاد فرم روی چرخ تنظیم، قطعه با فرم های دلخواه از قبیل مخروطی و شیار دار، سنگ زنی خواهد شد. این سنگ زنی برای اشکالی با سطح مقطع نامنظم مناسب است.
در سیستم های endfeed قطعه توسط استوپر در دو انتها نگه داشته شده و چرخ سنگ زنی و چرخ تنظیم روی آن اعمال نیرو میکنند. این چیدمان برای قطعات مخروطی مناسب است.
هونینگ یک فرایند سنگ زنی و پرداختکاری با سرعت پایین و کنترل شده است. در هونینگ ، برداشت مواد بوسیله حرکت برشی دانه های ساینده به هم چسبیده میله یا سنگ هونینگ انجام می شود. سیستم های هونینگ از چند سنگ چسبیده به یک استوانه هونینگ استفاده می کنند تا سطح داخلی یا خارجی قطعه را پرداخت کنند. این سیستم ها پرداختکاری بسیار ظریف و با دقت ابعادی بسیار بالا (در حد چند هزارم اینچ) روی سطوح داخلی و خارجی قطعات سیلندری انجام می دهند. حرکت میله هونینگ در این فرایندها به طور همزمان عمودی و چرخشی است و طرحی مانند هشت انگلیسی را روی قطعه ایجاد میکند. به دلیل سرعت پایین ، در این فرایند، مشکلات سطحی ناشی از افزایش دما در فرایند سنگ دستی مشاهده نمیشود.
شماتیک هونینگ
در کنار برداشت مواد و پرداختکاری ظریف ، هونینگ وظیفه اصلاح عیوب ناشی از فرایندهای ماشین کاری قبلی را نیز انجام می دهد. این اصلاحات شامل اصلاحات هندسی، اصلاحات ابعادی و مشخصه های سطحی می شود. شماری از عیوب متداول در ماشین کاری در تصویر مشاهده می شود.
انواع عیوب ماشین کاری
این فرایند برای طیف وسیعی از مواد، از فلزات نرمی مثل آلومینیوم گرفته تا مواد بسیار سخت مانند کاربید تنگستن استفاده می شود. سیستم استفاده از ذرات ساینده و چسبندگی آن ها در سنگ های هونینگ همانند چرخ سنگ زنی است.
هزینه سنگ زنی (جدا از هزینه های بالاسری) به وسیله سه فاکتور کنترل می شود. فاکتور اول انتخاب چرخ سنگ دستی است. کیفیت چرخ سنگ زنی ، تعیین کننده کیفیت سطح قطعه کار است و توسط ترکیبات ساینده مورد استفاده و اندازه ذرات کنترل می شود. هزینه سنگ زنی با ماده ای مثل آلومینا کمتر از روش های دیگر است اما سنگ زنی تمامی مواد با این ماده میسر نیست. انتخاب ماده جزئیات بسیاری دارد که کسب اطلاعات درباره آنها می تواند به انتخاب مناسب چرخ و کنترل هزینه سنگ زنی کمک کند.
فاکتور دوم انتخاب پارامترهای فرایند است. پارامترهایی از جمله سرعت فرایند و نرخ برداشت ، عمق برش و نوع مایع برش، روی کیفیت و هزینه سنگ زنی تاثیر می گذارند. برای مثال، نرخ برداشت مواد پایین موجب افزایش زمان فرایند و مصرف انرژی و در نتیجه افزایش هزینه سنگ زنی می شود. اما در نرخ سنگ زنی پایین، کیفیت پرداختکاری و دقت ابعادی سنگ دستی بیشتر می شود. بنابراین برای کنترل هزینه سنگ زنی باید تعادلی بین اقتصاد فرایند و کیفیت نهایی برقرار شود.
فاکتور نهایی کنترل هزینه سنگ زنی ، جنس قطعه کار مورد استفاده است. قابلیت سنگ زنی و پرداختکاری مواد مختلف عبارت از میزان سهولت برداشت مواد در این فرایند ها است. قابلیت سنگ زنی فولادهای ابزار سخت شده، در صورت وجود ذرات سخت کاربیدی کاهش می یابد. اضافه شدن درصد کمی گوگرد قابلیت سنگ زنی فولاد را افزایش می دهد. موادی با قابلیت سنگ زنی کمتر ، موجب افزایش سایش چرخ و در نتیجه هزینه سنگ زنی میشوند.
فرمت یک راه حل نوین جهت رفع نیازهای صنعتی است. هدف فرمت ایجاد بستری برای معرفی، بررسی و مقایسه ی خدمات صنعتی ارائه شده توسط ارائه دهندگان مختلف و انتخاب بهترین راه حل جهت رفع مشکلات و پاسخگویی به نیازهای صنایع مختلف است.
آدرس: تهران، خیابان آزادی، دانشگاه صنعتی شریف
ایمیل: info@formmat.ir