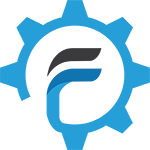
فرمت
محل ارائه خدمت: تهران
شماره تماس: 02191303797
فرمت » ساخت قطعات فلزی » ماشینکاری » فرزکاری و سنگ زنی » ماشینکاری اسپارک
تعداد ارائه دهندگان:
محل ارائه خدمت: اراک
شماره تماس:
[UAS_loggedin]
مشاهده
محل ارائه خدمت: تهران
شماره تماس:
[UAS_loggedin]
مشاهده
محل ارائه خدمت: تهران و اصفهان
شماره تماس:
[UAS_loggedin]
مشاهده
محل ارائه خدمت: تهران
شماره تماس:
[UAS_loggedin]
مشاهده
ماشینکاری اسپارک یا ماشینکاری تخلیه الکتریکی فرآیندی است که عمل براده برداری را به روش غیر تماسی و از طریق ایجاد جرقه روی سطح کار انجام می دهد. در فرآیند ماشین کاری اسپارک ، تخلیه الکتریکی توسط ژنراتور در مایع دی الکتریک انجام شده و جرقه های متناوب با ولتاژ پایین و آمپر بالا تولید می کند. دمای این جرقه ها از 8000 درجه تا 12000 درجه سانتیگراد متغیر است. میزان براده برداری دستگاه ماشینکاری اسپارک بستگی به انرژی جرقه دارد که چاله هایی با ابعاد از چند میکرون تا 1 میلیمتر تولید می کنند. زیاد بودن انرژی جرقه ها باعث افزایش سرعت فرآیند می شود اما کیفیت پرداخت سطح را کم می کند. در این فرآیند قطعه کار و ابزار به منبع الکتریکی متصل هستند و قطعه کار نقش کاتد و ابزار نقش آند را بازی می کند.
در ماشینکاری اسپارک ، قطعه کار معمولا روی صفحه ای درون محلول دی الکتریک قرار می گیرد. ابزار توسط سرووموتور (Servo motor) به صورت عمودی حرکت کرده و در فاصله از پیش تعیین شده ای از قطعه قرار می گیرد. در این فاصله، تخلیه الکتریکی ایجاد شده و عملیات ماشین کاری اسپارک شروع می شود. نقش سرووموتور کنترل فاصله بین قطعه کار و الکترود و ممانعت از ایجاد اتصال کوتاه بین این دو است. سرووموتور این کار را به وسیله مقایسه ولتاژ بین الکترود و قطعه کار با ولتاژ مرجع انجام می دهد. حین عملیات به دلیل خورده شدن قطعه کار فاصله بین قطعه و الکترود افزایش یافته و ولتاژ زیاد می شود. سیستم کنترل سرووموتور در هنگام انجام عملیات نیز فاصله را تنظیم کرده تا عملیات با قطعی مواجه نشود. در نقطه آغاز ایجاد جرقه بین الکترود و قطعه کار، فاصله بین این دو بین 0.4 تا 0.1 میلیمتر است. ایجاد جرقه توسط پالس های جریان مستقیم موجب ذوب و تبخیر قطعه کار و در نتیجه ایجاد حفره های کوچک می شود. در زمان قطعی پالس شستشوی براده ها و خارج کردن آن ها از منطقه جریان انجام شده و مایع دی یونیزه شده با مایع تازه جایگزین می شود. در هنگام ماشینکاری اسپارک یک نازل نیز مایع دی الکتریک را به وسیله شیلنگ روی محل ماشینکاری می پاشد تا براده ها با سهولت بیشتری از روی قطعه کار شستشو شوند. به دلیل این که الکترودها حین ماشینکاری تخریب می شوند، معمولا در هر مرحله ماشینکاری از چند الکترود استفاده می شود. آخرین الکترود نقش پرداخت نهایی سطحی را ایفا می کند. در پایان عملیات، مایع دی الکتریک آلوده به براده ها و ناخالصی ها که توسط شیلنگ به فیلتر فرستاده شده و تمیز شده است، به مخزن بر می گردد. در ماشينکاری اسپارک از منبع تغذیه خازنی مقاومتی و ترانزیستوری استفاده می شود. منابع خازنی مقاومتی نسبتا قدیمی تر بوده و از آن ها بیشتر در سوراخ کاری استفاده می شود. منابع تغذیه جدیدتر توان تنظیم زمان های قطع و وصل پالس ها را دارند که بین 2 تا 1000 میکروثانیه تنظیم می شود. جریان اعمال شده معمولا روی قطر حفره و زمان وصل بودن جرقه روی عمق حفره ها تاثیر دارد. سرعت ماشین كاری اسپارک در منبع تغذیه 125 آمپری تا حداکثر 410 میلیمتر مکعب در دقیقه می رسد. سرعت منبع تغذیه با ظرفیت 400 آمپر می تواند تا 4350 میلی متر مکعب در دقیقه برسد. معمولا در اغلب منابع تغذیه، پولاریته به صورت مثبت تنظیم می شود اما چنانچه در پالس های مشخص شده جریان معکوس اعمال شود، از چسبیدن الکترود به قطعه کار ممانعت به عمل می آید. جنس و کیفیت الکترودها یکی از عوامل تعیین کننده کیفیت نهایی و هزینه ماشینکاری اسپارک است. الکترودها معمولا از مس ، گرافیت و تنگستن ساخته می شوند. الکترودهای تنگستنی گرانتر هستند و بیشتر در برش وایرکات استفاده می شوند. در ماشین کاری اسپارک معمولا از مشتقات نفتی به عنوان مایع دی الکتریک استفاده می شود. از فواید مشتقات نفتی می توان به گپ کوچکتر، کیفیت سطحی مطلوب تر و سهولت بیشتر در حذف براده ها اشاره کرد. به طور کلی وظایف اصلی مایع دی الکتریک به این شرح می باشد. مایع دی الکتریک بایستی غیر رسانا باشد تا باعث باریک شدن پهنای کانال جرقه بشود. گرمای نهان تبخیر نیز باید به قدری زیاد باشد که موجب کوچک شدن قطر مایع تبخیر شده شود. همین مسئله به کوچک تر شدن قطر جرقه و افزایش کیفیت ماشینکاری اسپارک کمک خواهد کرد. همانطور که گفته شد جرقه ایجاد شده دمای بسیار بالایی دارد. مایع دی الکتریک بایستی خنک کنندگی بالایی نیز داشته باشد که موجب افزایش عمر الکترود شود. در نهایت مایع دی الکتریک باید به دور کردن براده ها از سطح ماشینکاری شده کمک کند. مایع دی الکتریک انتخاب شده برای انجام ماشینکاری اسپارک باید قطعه کار را تا حد ممکن فرسایش دهد اما تاثیری روی الکترود نداشته باشد. از سوی دیگر تاثیر منفی بر سلامتی نداشته باشد. در صورت برخورد با پوست بدن ایجاد مشکل نکند و گازهای سمی تولید نکند. هرچند با این شرایط نیز تعبیه سیستم تهویه در کارگاه ضرورت بسیاری دارد. نقطه اشتعال پایینی نداشته باشد چون مایعات با نقطه اشتعال پایین ایجاد گاز هایی می کنند که فرآیند ماشینکاری تخلیه الکتریکی را دچار اختلال می کنند و احتمال آتش سوزی را بالا می برند. چگالی بالایی داشته باشد تا عمل براده برداری به خوبی انجام گیرد. ویسکوزیته بالایی نداشته باشد تا به خوبی در چرخه مایع دی الکتریک جریان پیدا کند. در مقایسه با فرز CNC ، ماشینکاری اسپارک به دلیل نبود تماس بین قطعه کار و الکترود دقت ابعادی بسیار بالایی دارد و همچنین ایجاد اشکال ظریف و طرح های پیچیده و غیر متقارن را ممکن می کند. معمولا ماشینکاری های سنتی تر در ایجاد طرح های پیچیده با مشکل زیادی مواجه هستند. همچنین به دلیل ماهیت گرمایی این فرآیند، انجام ماشینکاری تخلیه الکتریکی روی قطعاتی که توان ماشینکاری پایینی دارند مثل کاربید ها یا فلزات سخت کاری شده ممکن می شود. از سوی دیگر ماهیت گرمایی فرآیند در کنار سرعت خنک شوندگی بالا، موجب سهولت در تراشکاری بدون اعوجاج قطعات بسیار نازک می شود. این روش توان ماشینکاری با دقت ابعادی دوازده هزارم میلیمتر را دارد. سطح ناشی از ماشینکاری اسپارک به وسیله مایع دی الکتریک کوئنچ می شود و ممکن است حاوی ترک های مویی باشد که به قطعه کار آسیب می رسانند. حذف لایه های سطح ذوب شده و حرارت دیده و افزایش استحکام خستگی سطح ماشینکاری شده معمولا به وسیله شات بلاست انجام می شود. همچنین می توان به وسیله پولیش کردن یا سنگ زنی لایه های متاثر از فرآیند را برداشت تا به مقاومت به خستگی بیشتر و کیفیت سطح بهتری دست پیدا کرد. بزرگترین محدودیت ماشینکاری اسپارک در جنس قطعات است. قطعات غیر رسانا به دلیل عدم تشکیل جرقه قابلیت ماشینکاری با این روش را ندارند. از سوی دیگر، ماشینکاری اسپارک کند تر از روش های ماشینکاری سنتی است و به دلیل مصرف انرژی بالاتر، افزایش مدت زمان فرآیند تاثیر بیشتری روی هزینه ماشینکاری اسپارک خواهد گذاشت. به طور کلی هزینه ماشینکاری اسپارک ، به خصوص به دلیل استهلاک الکترودها بیشتر از سایر روش های ماشینکاری است. همانطور که پیشتر گفته شد، دو متغیر اصلی تعیین کننده هزینه ماشینکاری تخلیه الکتریکی مصرف انرژی فرآیند و استهلاک الکترودها هستند. در صورتی که بتوان فرآیند اسپارک را در زمان کم و با حداقل مصرف مواد اولیه به انجام رساند، می توان به آن به عنوان رقیبی برای ماشینکاری های سنتی نگاه کرد. از این لحاظ انتخاب الکترود گرافیتی نه تنها باعث افزایش چند برابری سرعت فرآیند می شود بلکه با هزینه کمتر موجب کاهش هزینه ماشینکاری اسپارک نیز می شود. لازم به ذکر است که الکترود مسی هر چند گرانتر و کندتر است ولی پرداخت سطح بهتری ارائه می کند.نحوه عملکرد ماشینکاری اسپارک
منبع تغذیه در ماشینکاری اسپارک
الکترودهای ماشینکاری اسپارک
مایع دی الکتریک در ماشینکاری اسپارک
خصوصیات ماشینکاری اسپارک
هزینه ماشینکاری اسپارک
ساخت قالب کشش عمیق ساخت قالب پانچ ساخت قالب خمش ساخت قالب متالورژی پودر
فرمت یک راه حل نوین جهت رفع نیازهای صنعتی است. هدف فرمت ایجاد بستری برای معرفی، بررسی و مقایسه ی خدمات صنعتی ارائه شده توسط ارائه دهندگان مختلف و انتخاب بهترین راه حل جهت رفع مشکلات و پاسخگویی به نیازهای صنایع مختلف است.
آدرس: تهران، خیابان آزادی، دانشگاه صنعتی شریف
ایمیل: info@formmat.ir
2 Comments
تفاوت برش اسپارک با ماشین کاری اسپارک دقیقا توی چه مواردیه؟ آیا برش اسپارک رو هم انجام میدید؟
سلام
برای انجام خدمات برش اسپارک یا برش وایرکات به لینک زیر مراجعه کنید. در این مطلب جزئیات این فرآیند و هزینه های مربوطه هم به طور مفصل شرح داده شده.
برش اسپارک