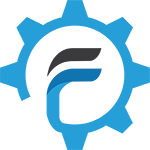
فرمت
محل ارائه خدمت: تهران
شماره تماس: 02191303797
فرمت » عملیات قبل/بعد از ساخت » عملیات حرارتی » سخت کاری » کربن دهی
تعداد ارائه دهندگان:
محل ارائه خدمت: کرج
شماره تماس:
[UAS_loggedin]
مشاهده
محل ارائه خدمت: تهران و اراک
شماره تماس:
[UAS_loggedin]
مشاهده
محل ارائه خدمت: تهران
شماره تماس:
[UAS_loggedin]
مشاهده
محل ارائه خدمت: تهران
شماره تماس:
[UAS_loggedin]
مشاهده
کربن دهی یکی از پرکاربردترین و ارزانترین روش های سختکاری سطحی است. این فرآیند در دسته اول روش های سختکاری فلزات گنجانده می شود زیرا ساختار کریستالی قطعه با نفوذ دچار تغییر می شود و ترکیب شیمیایی نیز تغییر می کند. کربن دهی شامل نفوذ کربن به یک فولاد کم کربن برای تشکیل یک سطح فولاد با کربن بالاست. اين فرآیند ضمن حفظ چقرمگی و استحکام مغز قطعه، سطح آن را نیز در برابر سایش مقاوم میکند. در این حالت سطح قطعه سخت و حجم آن نرم است.
عملیات کربن دهی برای افزایش مقاومت سایشی قالب های پرس مخصوص کارسرد و قالب سازی دایکاست استفاده می شود .این نوع قطعات بعدا نباید فرزکاری و سنگ زنی شوند زیرا لایه سطحی آنها از بین می رود. نام دیگر اين فرآیند، کربونیزه کردن است. در قدیم کربن را بصورت گازهای کربن دار روی سطح نفوذ می دادند مانند گاز کربن ناشی از ذغال چوب که به داخل قطعات آهنی نفوذ داده میشد و سپس سریع آن را سرد میکردند. امروزه قطعات آهنی را در یک محیط کربن دار ، با دمای بالا قرار می دهند و آن را گرم می کنند سپس با سرعت معینی دوباره سرد میکنند. در فرآیند کربن دهی ، قطعه مورد نظر با استفاده از یک ماده حاوی کربن مانند ذغالسنگ یا مونوکسیدکربن گرم میشود. حرارت دهی به قطعه در دمای 950-850 درجه سانتی گراد انجام میشود. درنتیجه این حرارت، فولاد کم کربن به منطقه دمایی آستنیت میرسد. فولادی که در این دما حرارت داده می شود، دارای ساختار آستنیتی پایدار است که در این حالت، حلالیت کربن زیاد می باشد. با افزایش پتانسیل کوره، یک شیب غلظتی بین محیط و سطح قطعه ایجاد میشود. در طی این فرآیند، در دو مرحله کربن به داخل سطح قطعه نفوذ میکند. مرحله اول جذب سطحی و مرحله دوم نفوذ کربن به داخل سطح می باشد. پس از آن، با سریع سرد کردن (کوئنچ کردن) یک ساختار مارتنزیتی در سطح بوجود می آید. هنگام کوئنچ کردن، غلظت بالاتر کربن در سطح خارجی از طریق تبدیل آستنیت به مارتنزیت، سخت میشود و مغز قطعه نرم باقی میماند. واکنش زیر در اين روش اتفاق می افتد: 2Co→Co2+C در فرآیند کربندهی میزان جذب کربن در سطح توسط دو پارامتر کنترل میشود: 1) واکنشی که بین اجزا تشکیل دهنده محیط (Co, Co2) و محلول جامد آستنیت انجام می گیرد. 2) سرعت نفوذ کربن از سطح به داخل آستنیت هرچه مدت زمان کربوراسیون طولانی تر و دمای آن بالاتر باشد، عمق نفوذ کربن بیشتر خواهد بود. فولادهایی که روی آن ها عملیات کربن دهی انجام می شود، فولادهای ساده کربنی و یا کم آلیاژ کم کربن هستند. می توان مقدار کربن در سطح این فولادها را می توان با استفاده از این روش افزایش داد. افزایش میزان کربن به حدی می باشد که ساختار سطح آن ها پس از کوئنچ کردن ، از دمای آستنیته شدن، به زمینه ی مارتنزیتی پر کربن با سختی بالا تبدیل می شود. پس از کربن دهی ، سطحی خواهیم داشت که نسبت به سایش و خستگی مقاومت دارد. در این فرآیند، میکروساختار مارتنزیت سخت پر کربن بر روی مغزی نرم و مقاوم به ضربه، به میکروساختار مارتنزیت کم کربن یا پرلیت و فریت تبدیل خواهد شد. فولادهای کربوره معمولاً حدود ۰٫۲٪ کربن دارند. به طور کلی محتوای کربن لایه کربندهی شده، در محدوده ۰٫۸٪ تا ۱٪ کنترل می شود. با این وجود، مقدار کربن موجود در سطح به ۰٫۹٪ محدود می شود زیرا مقدار زیاد کربن در این فرآیند می تواند باعث ایجاد آستنیت باقی مانده و مارتنزیت شکننده شود. کربن دهی فولاد معمولاً با روش های زیر انجام می شود: در بین این روش ها، روش های متداول در صنعت ایران سه روش جامد، مایع و گازی است. این دسته بندی بر اساس محیط کربن دهی و مواد کربن ده مورد استفاده در آن است. بر این اساس از سه گروه مواد جامد، مایع و گاز برای این فرآینداستفاده می شود. در کربن دهی به روش پودری یا جامد، قطعات فولادی را در جعبه ای که به “جعبه سمانتاسیون” معروف است، قرار می دهند و درون آن را از مواد کربن ده جامد پر می کنند. جنس این جعبه از فولاد نسوز می باشد. مواد کربن ده جامد موجود در جعبه باید هم کربن زا و هم انرژی زا باشند. مواد کربن زا که اغلب زغال چوب و یا کک می باشد و مواد انرژی زا مثل کربنات باریم، کربنات سدیم (سودا) ، کربنات کلسیم (پتاس) ، سود خشک و یا مخلوطی از آن ها می باشد که حدود ۲۰-۶ درصد مواد موجود در جعبه را تشکیل می دهند. وظیفه کربنات که یک عامل فعال کننده می باشد، تنظیم فشار و ترکیب گاز درون جعبه است. در آخر، جعبه را با مواد نسوز مانند آزبست یا خاک رس کاملا می بندند تا تبادلی با هوای خارج از جعبه رخ ندهد. جعبه را برای مدت زمان مشخصی در دمای ۹۲۵-۸۷۵ درجه سانتیگراد که دمای لازم برای کربن دهی می باشد، نگه می دارند. این زمان، وابسته به عمق سخت کاری مدنظر می باشد. نفوذ کربن به ازاء هر 9 میلیمتر است. واکنش انجام شده در این فرآیند به این صورت می باشد که اکسیژن موجود در جعبه، در ترکیب با زغال، co2 تولید می کند. با بالاتر رفتن دما، co2 تولید شده، با ذغال ترکیب شده و گاز co تولید می شود. در نتیجه این واکنش ها، گاز منو اکسید کربن تشکیل شده در سطح فولاد تجزیه می شود و کربن اتمی تولید می کند. همانطور که پیشتر گفتیم، کربن اتمی که درنتیجه تجزیه کربن منوکسید تولید می شود، جذب سطح فولاد می شود. این فرآیند، در دمای بالا یا منطقه تک فازی آستنیت ، اتفاق می افتد. در مرحله ای که کربن سطح فولاد سمانته افزایش می یابد، آن را سریع سرد می کنند. در حین کوئنچ کردن استحاله فازی آستنیت به مارتنزیت پر کربن در سطح فولاد انجام می شود. هنگامیکه کربن سطح افزایش می یابد، اصطلاحا می گویند که به آن آب داده شده است. کربن اتمی، با نفوذ به داخل فاز آستنیت، فاز سمنتیت را در لایه های سطحی فولاد تشکیل می دهد. روش کربن دهی جامد برای سخت کردن ابزاری مانند چرخ دندهها، بادامکها، میل لنگها، کاسه ساچمهها و زنجیرها استفاده میشود. در کربن دهی به روش گازی ، قطعه رادر محیطی که ترکیبی از گازها در آن وجود دارد، به مدت سه الی چهار ساعت قرار می دهند. در این روش، قطعات در اتمسفری حاوی كربن قرار دارد كه میتواند به صورت متناوب پر شود. متداول ترین منبع تولید کربن در کربونیزه کردن گازی ، گاز طبیعی (CH4) میباشد. اگر این گاز به تنهایی استفاده شود، بر روی قطعه دوده ایجاد می شود. دوده ایجاد شده بعلت غنی بودن گاز متان از هیدروکربن می باشد و مانع جذب کربن در سطح می شود. برای حل این مسئله، در کربورایزینگ گازی ، یک گاز حامل بنام گاز اندوترمیک که مخلوطی از هوای فشرده و گاز طبیعی میباشد را به نسبت ۲ به ۱ و در دامنه حرارتی ۱۰۴۰ تا ۱۲۰۰ درجه از یک بستر نیکل عبور می دهند. نیکل به عنوان کاتالیزور واکنش می باشد. در این فرآیند ، از یک محفظه غنی از کربن مایع استفاده می شود و قطعات در آن غوطه ور می شوند. سیانور، جز اصلی حمام های کربن دهی مایع می باشد. قطعات را در نمکی مذاب تا حدی نگه می دارند که کربن به سطح فولاد نفوذ کند. این مذاب شامل کربنات سدیم، نمک سیانید سدیم و نمک طعام، کلرید باریم و سیلیسیم کاربید است. با خنک سازی سریع (کوئنچ کردن) یک پوسته سخت تولید می شود. سطحی که توسط کربوراسیون مایع سخت می شود، مقدار کمی نیتروژن و مقدار زیادی کربن دارد. درجه حرارت در فرآیند کربورایزینگ مایع حدود ۸۵۰ درجه سانتیگراد می باشد و زمان مورد نیاز بسته به میزان نفوذ مورد نظر و درجه حرارت، بین ۳۰ دقیقه تا ۴ ساعت میتواند تغییر کند. دو روش برای سنجش ضخامت لایه سخت شده در روش های کربن دهی داریم کربن دهی بخصوص به روش گازی ، امکان مکانیزه و اتوماتیک شدن دارد و درنتیجه نیاز به نیروی انسانی کاهش یافته و هزینه کربن دهی نیز کاهش می یابد. همچنین این روش سریع بوده و از طیف وسیعی از کوره ها برای انجام عملیات میتوان استفاده نمود. درنتیجه این موارد باعث می شوند فرایند کربندهی به صرفه بوده و از لحاظ اقتصادی نیز توجیه داشته باشد.فرآیند کربن دهی
فولاد های کربوره
روش های سخت کاری کربن دهی
کربن دهی جامد
تغییر ریزساختار در فرآیند کربن دهی جامد
مزایای کربن دهی جامد
معایب کربن دهی جامد
کربن دهی گاز
در کربوراسیون گازی ، گاز را سریعا تا دمای ۳۱۵ درجه سانتیگراد سرد می کنند تا دوده تشکیل نشود. بنابراین برای اتمسفر کوره، از یک گاز اندوترمیک به عنوان حامل و یک هیدروکربن مانند متان یا پروپان به عنوان عامل کربن زا استفاده می شود. برای جلوگیری از نفوذ هوا به داخل کوره باید آن را طوری تنظیم کرد که فشار گاز داخل کوره بیشتر از فشار اتمسفر باشد.مزایای کربوراسیون گازی
معایب کربوراسیون گازی
کربن دهی مایع
مزایای روش کربوراسیون مایع
معایب روش کربوراسیون مایع
سنجش ضخامت لایه سخت شده به روش کربن دهی
1) روش متالوگرافی : قطعه سخت کاری شده به روش کربندهی را مقطع زده و لایه کربوره ر زیر میکروسکوپ نوری و یا توسط یک ذره بین، اندازه می گیرند.
2) روش آزمون میکروسختی : قطعه مورد نظر، پس از سختکاری مقطع زده شده و مقطع نمونه از سطح به مغز با نیروی بسیار کم توسط روش ویکرز، سختی سنجی میشود. نمودار پروفیل سختی بر حسب فاصله از سطح قطعه رسم میشود تاجایی که سختی ۵۵۰ ویکرز شود. آن نقطه را می توان ضخامت لایه کربوره در نظر گرفت.هزینه کربن دهی
فرمت یک راه حل نوین جهت رفع نیازهای صنعتی است. هدف فرمت ایجاد بستری برای معرفی، بررسی و مقایسه ی خدمات صنعتی ارائه شده توسط ارائه دهندگان مختلف و انتخاب بهترین راه حل جهت رفع مشکلات و پاسخگویی به نیازهای صنایع مختلف است.
آدرس: تهران، خیابان آزادی، دانشگاه صنعتی شریف
ایمیل: info@formmat.ir